Preventive Maintenance Checklist of Cone Winding Machines of Sewing Thread in Textile
Cone winding is a finishing process of yearning or sewing thread packaging. A cone winding machine is a piece of equipment used in textile and sewing industries to wind sewing thread onto cones or spools. It is an essential part of the thread manufacturing process, as it allows for efficient and uniform winding of thread onto larger storage units. Here we go details Maintenance Checklist of Cone Winding Machines in the Textile industry below.
Performing regular preventive maintenance on cone winding machines for the sewing thread finishing process is crucial to ensure their optimal performance, prevent breakdowns, and prolong their lifespan. Here’s a general checklist of preventive maintenance tasks for cone-winding machines. It’s important to note that this checklist is a general guideline, and specific maintenance requirements may vary depending on the manufacturer’s recommendations and the unique characteristics of the cone winding machine you are using.
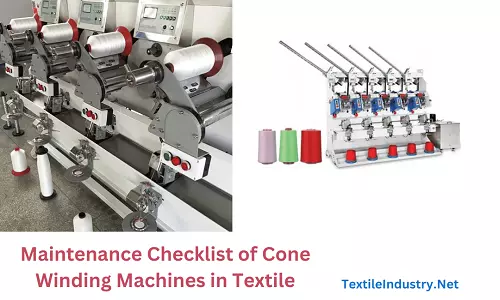
Preventive Maintenance Checklist of Cone Winding Machines
Sl. No. | Maintenance checklist |
1 | Spindle thorough checking and cleaning (a) Yarn crill (b) Inlet Ceramic Eyelet and Bar (c) Loop Catcher (d) Magnetic Yarn Tensioner & o ring. (e) Outlet Ceramic Eyelet (f) Oil Aplicator, Inlet & outlet Ceramic Guide. (g) Yarn Detector (h) Yarn Barcket (i) Yarn Displacement Drum (j) Clean Bail Roller & Supporter |
2 | Cam alignment check and cleaning ( Disassemble, cleaning, assemble and adjust) |
3 | Timing Belt adjusment checking and cleaning |
4 | Bail roller & Supporter alignment adjusment and cleaning |
5 | Timing Belt adjustment checking and cleaning |
6 | Sensor ( yearn, door, empty tube) adjustment and functionalize. |
7 | Electrical cabinet ( back side) cleaning. |
8 | Air regulator checking and cleaning ( filtr functionalize) |
9 | All control and power cable tightness checking ( 48V & 24V cable & connector replacement) |
10 | Right Flange Checking & Cleaning ( Rubber bucket,o -ring Spring, replacement and adjustment) |
11 | Driving Head cleaning and checking ( Spring, Bearing, Distancebust, replacement) |
12 | Doffer checking, Cleaning & maintenance ( Axial Bearing, Brush Bush, cylinder+blind, Scissor, cone holder adjustment ) |
13 | Machine calibration & Recalibrate ( Diameter) |
14 | Door Lock Checking & Maintenance ( Cable with connector replacement & position adjustment) |
15 | Lube applicator cleaning ( each component disassemble, cleaning & assemble, communication cable replacement) |
16 | PLC card cleaning ( electronics card disassemble, cleaning, heating, and fixing) |
17 | Lube line cleaning ( lube drum, lube line fitting, pump & cable replace & joint pipe- 16 mm replacement |
18 | Electrical Panel cabinet cleaning. |
19 | Checking of Compressed air line Leakage |
20 | Availability of Blind in Pneumatic Line (Where Applicable) |
Conclusion
Cone winding machines vary in size, capacity, and features depending on the specific requirements of the textile industry. They can be manual, semi-automatic, or fully automatic, offering different levels of control and productivity. But the Preventive Maintenance Checklist of Cone Winding Machines is the same.
- You may love to read: Sewing Machine Maintenance Checklist and Technical Adjustments
- Difference between Yarn and Thread; Yarn vs Thread