Denim Finishing using Laser Technology- A detailed study on the working process of laser machine
The industry is moving toward 4.0, by matching the footstep the garment industry is also moving toward 4.0. Denim washing is also not behind in this race. Denim washing is moving toward sustainability. Laser is a milestone to that path only. Making a pair of denim is labor-intensive work and takes a long time. Laser makes this process effortless. Laser can finish a pair of jeans in 90 seconds, compared with up to 20 minutes for hand finishing. Here I present Denim Finishing using Laser Technology: and the working process of the laser machine.
The Traditional Denim Finishing Process: Before delving into the innovative use of Denim Finishing using laser technology, let’s briefly examine the traditional denim finishing process. Historically, denim finishing involved labor-intensive techniques such as sanding, scraping, and hand brushing to create distressed or worn-out effects. This process was not only time-consuming but also generated significant waste, posing environmental concerns.
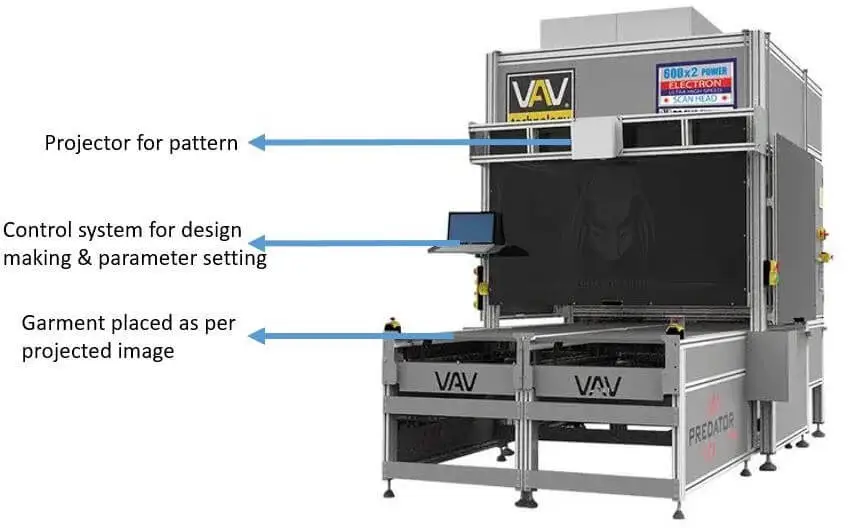
Process Flow Chart of Laser department
Receiving from Input Garment Store |
↓ |
Size wise segregate (Inseam length) |
↓ |
Send to the machine |
The technician calibrates the laser machine parameter as per design & inseam length |
Technician calibrate the laser machine parameter as per design & inseam length |
↓ |
Operator put the garment according to the projection on laser table |
↓ |
Put metal plate to avoid the unnecessary printing & movement of garment |
↓ |
Laser come into action & do the print on garment |
↓ |
Quality team inspect the 1 piece for each size |
↓ |
Operator do a visual check & put the next garment on laser table |
Initially, hand sand & whisker is done manually. There is a chance of variation from garment to garment. Once laser technology comes into action the variation is reduced to a significant level. A laser can complete this process in 90 seconds compared with up to 20 minutes in hand finishing.
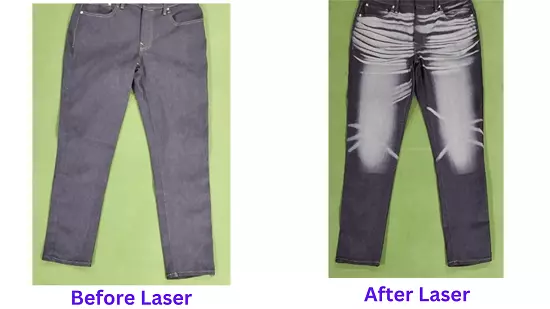
Machine Calibration Process:
There are three main machine parameters which decide the performance of the laser machine:
- Laser Power: This is the value that adjusts the laser power. It is expressed as a percentage. It is important to use the laser power at max level so that the machine can be used efficiently. Laser power doesn’t increase the laser burning speed but it will help to reduce time for another parameter which in turn increases efficiency.
- Max Exposure time: This is the indication of the maximum waiting time of a laser beam on a point. With this parameter, the burning power can be adjusted. When max Exposure time is increased the burning time also gets increased so burning will slow down & efficiency will be reduced. Once max exposure time is reduced the burning time will increase & efficiency will also increase.
- DPI: Dot per inch, means the number of dots available in an inch of area. DPI value is the parameter that affects the burning power. When DPI gets increased the burning power also gets increased but the burning time gets slow. Burning at a slow speed is a loss for production. So a standard DPI value should be chosen so that quality & quantity are not compromised.

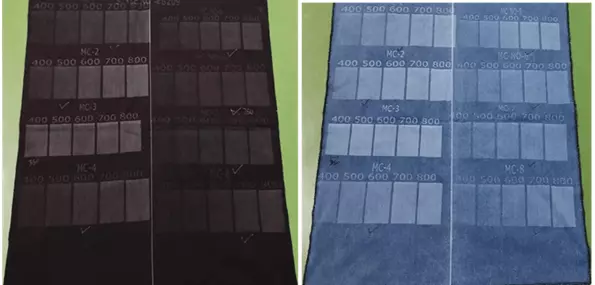
A few Observation about Laser Machines:
- Different fabric behavior is different in the same machine parameter.
- Even in the same fabric, the same intensity but different machine shows different results.
- Need to confirm machine-wise parameters for the consistent results of the garment.
Size wise segregate (Inseam length)
Inseam length wise garment need to separate before feeding in the machine. As in many brands, it has been found that in one waistband three different sizes of inseam have been found. So it is very important to separate the size. Below is the inseam size & waistband size relation:
Inseam | Waist band Size |
28 | 26-28 |
30 | 29-30-31 |
30 | 32-33-34 |
Garment Feeding on Laser Table:
Feeding the laser machine is another critical work. There is a projector present in the laser machine. The projector makes an image in the feed plate. Garments need to be placed properly to get them printed. If the placement is wrong, then the garment will be rejected as the laser will print in the wrong place. Once the laser is printed there is no chance to make it correct. Feeding position of the laser:
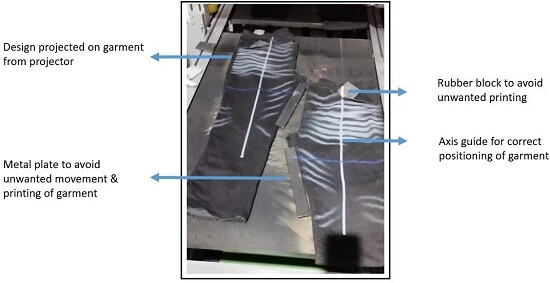
Advantages of Denim Finishing using Laser Technology
The introduction of laser technology into denim finishing has completely redefined the industry. Here’s how it works and why it’s a game-changer:
- Precision and Consistency: Laser technology allows for precise control over the finishing process. Designers and manufacturers can create intricate patterns, fades, and distressing effects with unmatched accuracy, ensuring consistency across denim garments.
- Sustainable Innovation: Perhaps the most significant benefit of laser finishing is its sustainability. Unlike traditional methods that require excessive water and chemicals, lasers produce minimal waste and have a significantly lower environmental impact. This aligns perfectly with the growing demand for eco-friendly fashion.
- Speed and Efficiency: Laser technology reduces production time and costs. It eliminates the need for time-consuming manual labor, thereby increasing the efficiency of denim manufacturing processes.
- Customization and Creativity: With laser technology, the possibilities are limitless. Designers can experiment with a wide range of effects, from vintage fades to intricate patterns, to cater to diverse consumer preferences. Customization becomes more accessible, empowering brands to offer unique denim products.
- Worker Safety: Traditional denim finishing processes, involving chemicals and abrasive materials, can pose health risks to workers. Laser technology minimizes these risks, creating a safer work environment.
Conclusion
Denim jeans are among the most popular articles of clothing on the planet. 4.5 billion pairs of them were sold in 2018 alone, meaning that at any given moment, approximately half of the entire global population is wearing these convenient, hard-wearing, and stylish trousers. One study showed that, To begin with, jeans consume a lot of resources. In order to grow sufficient cotton to create just one pair of denim trousers, 1,500 gallons of water are consumed. Yet not end, once we bring the pair of jeans & wash it at home the pollution is not stopped. Another research revealed that just one wash could be responsible for the release of 50,000 individual microfibers.
Denim Finishing using Laser Technology, Laser wash is the best solution to avoid all this pollution & make the denim wash sustainable. Apart from that the number of workers is reduced significantly & make a wide range of designs with this laser. The more we move toward sustainability more we need to grow interest in laser to make the world a better place.
- Author: Sourav Ghosh
- Masters from NIFT Delhi in fashion Technology, B.Tech in Textile Technology From GECTTS (2012-2016) EX- Arvind Mill
- Email: [email protected]
- You May Love to read: Difference Between Denim and Jeans
- Top 10 Denim Jeans brands in World
- 10 Interesting Facts about Denim and Jeans You need to know
- 7 Diverse Uses of Denim Fabric