Technical Audit Checklist in the Sweater Industry
A sweater production industry has many operations: Yarn winding, Knitting, Linking, embroidery, Pressing, Finishing – Packing are the key sections. All the operations are technically sensitive. A technical audit checklist ensures quality requirements and standard level. This article presents a Technical Audit Checklist in the Sweater Industry.
A technical audit is a technical examination as per requirements of quality standard. These Technical Audit Checklist in the Sweater Industry will help a factory assessing QMS system.
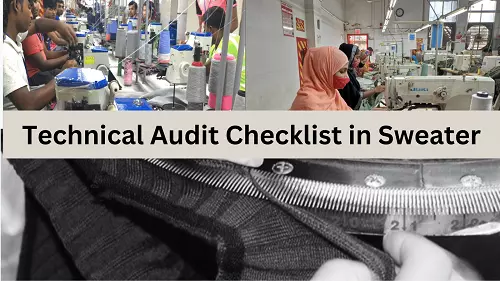
A Detail of Technical Audit Checklist in the Sweater Industry
Here, section by section Technical Audit Checklist in the Sweater Industry described:
section | Technical Audit Checklist in the Sweater |
01 Warehouse | 1. Is the warehouse clean & in good condition? |
01 Warehouse | – warehouse is indoor, wall / roof / floor without holes; floors are marked; – sufficient racks / pallets, 0.5-1 meter from wall; – proper aisles in between the racks /pallets; -All windows are installed with window screen. – Gauze net should be installed on the external openings, air-vents or exhaust fans. – All external doors are installed with gauge curtain. – Cover all open boxes at warehouse – Invite a licensed 3rd party company/agency to do pest control in whole factory at least once a year. o Keep the copy of certificates and licenses of the pest control provider for 1 year. o Keep records such as regular visit logs, documentations of chemicals used, work completed, observations of activity and recommendations for 1 year. |
01 Warehouse | Environment is acceptable to keep material good for a few months’ time. |
01 Warehouse | Found any material is wet, dusted or mold. |
01 Warehouse | The environment cannot protect material from damage. |
01 Warehouse | 2. Randomly select 1 style from WIP to check if it has material test report and appropriate inspection processes are used. |
01 Warehouse | – Buyer approved shade, hand feel, color band, are available and referred during inspection. – The inspection process is appropriate checking yarn strength, evenness and tex for every bulk lot. – Inspectors are well trained and had taken color blind test. – Proper inspection machine are used. – Inspection work station is 800-1000 lux. |
01 Warehouse | Same as Good while random check bulk lot. Not every lot. |
01 Warehouse | Anything listed in questions are missing or needs improve. |
01 Warehouse | No testing machine, no report or no inspection on site. |
01 Warehouse | 3.Are all storages, including raw materials/finished goods/Vendor Manage Inventory (VMI)/leftover/rejected goods, organized and stored indoors, off the floors and remain covered (light color) / protected with clear label until ready for use? |
01 Warehouse | – All are stored by lots, by color by order / delivery in an organized way so even new workers can perform. – Factory has sufficient space and racks / pallets, and with good house keeping; if on pallets, goods are at reachable height; – light color are covered; – clear indication of buyer/ style / items on rack and location systems where all warehouse staff can easily identify. |
01 Warehouse | – All storage are clearly labeled and in good condition. |
01 Warehouse | – found storages are not organized or in poor condition so immediately corrections is needed. |
01 Warehouse | – No sufficient space and overall is poorly organized storage. – more than 50% of material are contaminated due to poor storage environment. |
01 Warehouse | 4.Is light box and approved shade band available with qualified colorist for bulk color verification? |
01 Warehouse | – Approved shade band for bulk color verification is well done and record well kept. – Gap approved light box is used. – Gap brands’ light source list is posted outside the light box. – Light box is calibrated yearly. – Light tube & bulb usage hours is monitored and replace less than 2000 hrs. – 45 degree triangle is used for shiny fabric only. – Checker qualified by passed 3rd party lab test (Munsell test) in yearly basis. • Colorist = Superior Discrimination (Error score of 0 to 16) • DA/QA/Inspector = Average Discrimination (Error score of 20 or below) • Failed = Low Discrimination (Error score of more than 20) |
01 Warehouse | – Approved shade band for bulk color verification is well done and record well kept. – Gap approved light source per brand is used. – Gap’s light source list is posted outside the light box. – Light box is calibrated but not updated. – Light tube & bulb usage hours are not monitored. – Checker passes internal Munsell eye test or color blind test in yearly. For new factory, if no meet above, as long as factory agrees to buy the light source upon order placement. this sb put in comment in TE report for approval letter. |
01 Warehouse | any of the criteria listed in accept rating is insufficient. |
01 Warehouse | – There is no light box./ non-function light box. – No Fabric color checking by light box. – There is no buyer standard/ color standard, only factory internal sign off standard. – no identified person for color checking. |
01 Warehouse | 5. Randomly select 1 style from WIP to check if it has complete and clear trim card with approval in all related departments. |
01 Warehouse | – There is a complete and clear trim card with buyer’s approval – The signature can be by factory merchandiser / FKR/VKR or GSS staffs. (with clear signature, name & date or email copy in the file) – the trim card is accessible for all workers/ supervisors/ QC to use in all depts. |
01 Warehouse | There are correct and represent bulk quality material ( not bulk ) available in warehouse and all dept QC. |
01 Warehouse | missing info in trim card or not enough trim card production areas. |
01 Warehouse | no trim card prepared. Only photo copies of trim card used. |
01 Warehouse | 6.Are all materials stored indoors ? |
01 Warehouse | All material is stored indoor and not exposed to sunlight and rain |
01 Warehouse | All production material is stored indoors, just leftover material is put outdoors with covers. |
01 Warehouse | There are less than 20% of material are store outdoors or covers without walls. |
01 Warehouse | More than 20% of materials are storage outdoors. |
01 Warehouse | 7.Are rejected bulk lots being separated and put under quarantine? |
01 Warehouse | – Rejected lots of raw materials / trims / parts are clearly marked and put into designated area / boxes. – Separated rooms or locked containers from the remainder of bulk with clear record; – assigned person were responsible for allocation and separate these from good product, limited access to all workers. |
01 Warehouse | – Rejected lots of raw materials / trims / part are clearly marked but stored were not locked. – There is no designated person to handle these rejected lots. |
01 Warehouse | – Rejected raw materials were put in designated area with open cover boxes. – There is high possibility of mix those rejected from the good products in packing. |
01 Warehouse | – Found rejected lots are mixed with the rest of the bulk in packing and not clearly marked. |
02 Yarn winding – Knitting | 1. Is the winded yarn in correct threading, tension and consistently on similar weight and circumference across all cones with clear label? Is the winding of white and light shaded yarn separated from dark colors? (take pictures of Yarn Cones in the Winding area both Before and After re-Winding/Re-Waxing’) |
02 Yarn winding – Knitting | The winded yarn are in correct threading, tension and consistently on similar weight and circumference across all cones with clear label. The winding of white and light shaded yarn separated from dark colors. or the incoming yarn is good enough without re-winding. |
02 Yarn winding – Knitting | less than 20% deviation from Good Process while bulk quality could still pass Final |
02 Yarn winding – Knitting | more than 20% missing and bulk quality is at risk to fail |
02 Yarn winding – Knitting | none is available or the setting is so poor that it is same as nothing available |
02 Yarn winding – Knitting | 2. Is knit panel total length checked with tension checking machine every two hours? |
02 Yarn winding – Knitting | – There is knit panel total length checking procedure per machine once every two hours and with the clear record upon daily routine. |
02 Yarn winding – Knitting | – There is knit panel total length checking by identical person per shift once a time. Clear record. |
02 Yarn winding – Knitting | there is insufficient knit panel total length checking or unclear record. However, there is checking per style per color. |
02 Yarn winding – Knitting | there is insufficient knit panel total length checking in style basis or no record of checking. |
03 Linking | 1. Is the approved sample available in the sewing line ? |
03 Linking | Approved sample hanging at each sewing line with clear and complete hangtag. with approval signature and buyer comments. The samples are the same style of the one producing in the sewing line. |
03 Linking | All styles have approved samples in sewing area but it is not easy to access by workers or QC or not putting per sewing line. |
03 Linking | Any styles found missing sample. |
03 Linking | 50% of styles missing sample. or approved samples are not those styles in production. |
03 Linking | 2.Are pilot runs conducted prior to bulk production with a record ? What is the action taken for pilot runs that do not meet our standard? |
03 Linking | – Pilot run is conducted for every color, full size set in bulk production lines. – Clear record – There are follow up actions for failed product in time. |
03 Linking | – Same as Good Rating while Pilot run is conducted for light/dark color, jump size set, but not conducted in bulk production lines. |
03 Linking | – Pilot run is conducted in either 1 color, jump size. – incomplete follow up actions for failed products. |
03 Linking | – No pilot run process in the factory. – no actions for failed product. |
03 Linking | 3. Randomly select 3 sewing machines (different operations if possible & critical operations are preferred) to check - If calibration/maintenance records are well kept – If the stitching is good – If there is UBT or wipers, if there is LED or light |
03 Linking | – Machines are set properly before operation and maintained regularly to ensure consistency. – Maintenance record is well kept. – Good wiring – calibration with record. with correct folders and light. 80% machines are automatic machines. |
03 Linking | Same as 3 while record is not well kept. – machine function is fair – maintenance / wiring is acceptable. |
03 Linking | – machine maintenance is barely acceptable and need further improvement; |
03 Linking | – Machines are not properly maintained – Maintenance record is not well kept. – Poor wiring |
03 Linking | 4.Is there a proper maintenance department equipped with adequate tools and necessary equipment to support and make trolley, side table, tray, support shelf, rack, pulley, roller……etc.? |
03 Linking | – There is a technical team/ industrial engineer to design suitable working tools. – Maintenance depts. are fully equipped with adequate tools and equipment – The tools and equipment are being utilized effectively/efficiently |
03 Linking | – tools that order from external source are adequate. |
03 Linking | – there is inadequate tools used in the production. |
03 Linking | -No equipment. |
03 Linking | 5.Can floor supervisors/QA show how to check visual and measurement? |
03 Linking | All supervisors can demonstrate correct checking method. |
03 Linking | Only the QC manager and QA can demonstrate correct checking method |
03 Linking | Some of them show mistake in either visual or measurement. |
03 Linking | No inspector at factory can show. Only the Final inspector knows. |
03 Linking | 6. Is the sewing workshop clean & in good condition? ** focus on the areas that will affect product quality. |
03 Linking | All sewing machines are free of stain and dirt. Working stations are clean, not broken, no sharp edges. Racks are clean. |
03 Linking | All are clean. Even some machines/ stations/ racks looks old, there is no dirt/stain that could contaminate product. |
03 Linking | Found there are stain/ dirt in environment that contaminate product or found dirt in Final inspection report. |
03 Linking | Most areas are dirty. Many products are getting dirt and needs to be cleaned before pack. |
03 Linking | 7.Is there any system & instrument available for checking the linking yarn strength before release to workers? |
03 Linking | Linking yarn is tested by lot by delivery and with clear identification and traceability. |
03 Linking | There is 10% or above sampling size of linking yarn per lot is tested for yarn strength by manually and with clear records. |
03 Linking | – <10% linking yarn strength is checked manually with clear record |
03 Linking | – No checking or no record or tested and linking yarn is not strong enough. |
03 Linking | 8.Are linking worker skillful? |
03 Linking | More than 80% of the works are skillful and machines runs smoothly and fast. |
03 Linking | 79-60% of the works are skillful and machines runs smoothly and fast. |
03 Linking | 40-59% of the works are skillful and machines runs smoothly and fast. |
03 Linking | Less than 40% of the works are skillful and machines runs smoothly and fast. |
03 Linking | 9. What is the ratio of table checker vs. linking workers? Is it 100% check and mend before washing? |
03 Linking | – Ratio: 1 to 25 or below – 100% checked |
03 Linking | – Ratio: 1 to 26-35 – 100% checked |
03 Linking | – Ratio: 1 to 36-50 – 50% randomly checked |
03 Linking | – Less than 50% random check, ratio more than 1:50 |
03 Linking | 10. What is the ratio of lamp checker vs. linking workers after linking ? Is it 100% check? |
03 Linking | – Ratio: 1 to 25 or below – 100% checked |
03 Linking | – Ratio: 1 to 26-35 – 100% checked |
03 Linking | – Ratio: 1 to 36-50 – 50% randomly checked |
03 Linking | – Less than 50% random check, ratio more than 1:50 |
03 Linking | 11.Is the ratio of the Mending/ Stitching workers to Linking workers appropriate based on the production and the complexity of the styles? (Line balancing). |
03 Linking | Yes, well set up for every line balancing for separate style. |
03 Linking | Yes, around 80% is well set up. |
03 Linking | Insufficient ratio and found > 20% is not well set up. |
03 Linking | Everywhere seems accumulated and less than 50% is well set up. |
03 Linking | 12.Is there effective traceability system to monitor product quality and worker performance? |
03 Linking | Bar code or electronic chip are used in monitoring each operator’s output and quality. Roving QC/inline QC also key in the defects by computer. There are real time tracking. |
03 Linking | Use manual check with clear report. Not real time but can track in daily basis. |
03 Linking | Limited manual tracking where reports released >1 day period. |
03 Linking | only with manual checking , no report. |
04 Pressing – Finishing – Packing | 1.Does factory use appropriate pressing/ heat setting equipment, template and guides to ensure pressing consistency? |
04 Pressing – Finishing – Packing | -All pressed product are consistence in shape and visual. -Factory uses correct pressing equipment for different products. – The equipment are well maintained without leaking water/steam, steam pressure should steady. – Vacuum/oven function properly. – irons are suspended by springs to avoid damage garment – Correct templates use. – Pressing machines are clean – Steam pipes/ electric wire/ iron are wrapped properly. |
04 Pressing – Finishing – Packing | 80% of equipment are clean and well maintained while all products are in good pressing quality. |
04 Pressing – Finishing – Packing | More than 20% equipment are worn or insufficient. |
04 Pressing – Finishing – Packing | More than 50% equipment are worn or insufficient. |
04 Pressing – Finishing – Packing | 2. For same style, are all operators use same garment pressing method for same style? |
04 Pressing – Finishing – Packing | – All operators working on same style in same procedure – Vacuum suction is properly used – Use correct template – Pressed product should not piled over 12″/30 cm – supervisors using the daily defect % to monitor operator’s performance – operator should adjust the product shape, then pressing, then use vacuum. They cannot press the vacuum all the time which lead to shape distortion. Especially for sensitive / sweater/knit product. |
04 Pressing – Finishing – Packing | 80% of operators are in same pressing procedure while all products are in good pressing quality. |
04 Pressing – Finishing – Packing | more than 20% product in poor pressing quality. |
04 Pressing – Finishing – Packing | More than 50% product in poor pressing quality. |
04 Pressing – Finishing – Packing | 3.Is there inspection before packing in visual, measurement and shading? |
04 Pressing – Finishing – Packing | 100% check visual & critical POM in measurement after pressing. ‘clear report and immediately correction on process to rectify defects by supervisor |
04 Pressing – Finishing – Packing | 100% check visual & critical POM in measurement after pressing. |
04 Pressing – Finishing – Packing | only check randomly or based on AQL sampling on visual and measurement. |
04 Pressing – Finishing – Packing | No checking, no clear separation of 1st quality and defectives. |
04 Pressing – Finishing – Packing | 4. Are there enough trolleys to hold the after pressing goods instead of putting in large bins? Is there appropriate time to dry prior to packing? |
04 Pressing – Finishing – Packing | 100% garment placed nicely at the trolleys. |
04 Pressing – Finishing – Packing | less than 20% garments are placed on table as not enough trolleys. |
04 Pressing – Finishing – Packing | Found there are 20-50% high piled up products as there are not enough trolleys. |
04 Pressing – Finishing – Packing | More than 50% high piled up products found. |
04 Pressing – Finishing – Packing | 5. Are packaging standard and samples readily available for reference? |
04 Pressing – Finishing – Packing | – Clear instruction with supervisor signed. Folded sample displayed per table. |
04 Pressing – Finishing – Packing | – correct packed sample or instruction displayed per table. |
04 Pressing – Finishing – Packing | – Packed samples for current packed styles with instruction stored at supervisor desk. Workers can review when needed. |
04 Pressing – Finishing – Packing | – Missing/ Incomplete / No instruction |
04 Pressing – Finishing – Packing | 6. Is the packing material released in control way to avoid mixing and mistakenly packed? |
04 Pressing – Finishing – Packing | – The packing material is released per operator per daily consumption with ZERO wastage. – packing area should be separate by PO shipping country. – clear residue of leftover location is marked at packing stations. – 1 operator only pack 1 size/color/style at one time. |
04 Pressing – Finishing – Packing | – Same as 3 while – clear separation of packing material per size/color/style sharing with multiple operators |
04 Pressing – Finishing – Packing | – The packing material is released in style/PO basis at packing section. – no rack/box/divider to separate the packing material per size/color/style. Easy to be mixed. |
04 Pressing – Finishing – Packing | – No control, packing worker can access to all packing material any time. |
04 Pressing – Finishing – Packing | 7.Is the folded size and size sticker consistent? |
04 Pressing – Finishing – Packing | -Folded size and size sticker are consistent. Pile height less than 12″, stored by style/lot/color and is labeled clearly at racks or shelves and covered for overnight. |
04 Pressing – Finishing – Packing | Folded size and size sticker are consistent. Pile height is around 12″, stored by style/color/ and is labeled clearly at rack or shelves. Covered over night. |
04 Pressing – Finishing – Packing | – Pile height over 12″ – Stored with unclear label but have arranged per style/lot/color. Some fold size and or size sticker can further improve. |
04 Pressing – Finishing – Packing | – Mix color/ style – Pile height over 12″ – No label |
04 Pressing – Finishing – Packing | 8. Is there a procedure in place to remove stain, loose threads and foreign materials? Are defects found recorded and reported to sewing production? |
04 Pressing – Finishing – Packing | – Clear standard/procedure is given. – All workers are given the same tools <e.g. thread end sucker, blazer with sucker, vacuum, and princes> with procedure to follow – Clean bulk are checked and passed. – Clean QC and worker’s table – finished products are free of stain and thread ends. |
04 Pressing – Finishing – Packing | – All workers have similar process/ tools. – Cleaned bulk is checked and passed. |
04 Pressing – Finishing – Packing | – All workers are in different process – Lack of understanding between sewer & trimmer on loose threads. – Some bulks are checked and found thread ends untrimmed in minor defects.”- All workers are in different practice – Lack of partnership between sewing workers & trimming workers on loose threads. – checked some product found thread ends or minor defects.” |
04 Pressing – Finishing – Packing | – Found trimming area not organized so mixing trimmed and untrimmed products. Areas are dirty with threads on garments. |
04 Pressing – Finishing – Packing | 9.Is there an effective stain removal management and repair operation? |
04 Pressing – Finishing – Packing | – The cleaning section is well equipped (e.g. compressed air gun, vacuum, non toxic cleaning flute, mask, tap with running water) – Air ventilation is good with exhaust fan – Repairing work is well organized with clear separate of good and defectives. – exhaust fan with enough suction of fumes to outside. – Lighting is adequate (800-1000) lux – correct MSDS display |
04 Pressing – Finishing – Packing | – Either equipment / environment / organization are not as good as Good rating – Found some styles have mixed the good & defectives product. – Lighting is out of 800 – 1000 lux |
04 Pressing – Finishing – Packing | 10. Are the pressing & finishing workshops clean & in good condition? |
04 Pressing – Finishing – Packing | 100% clean tools and tables, storage buckets, racks and areas. Pressed garment should fold properly and pile up not more than 12″. 1. Mosquito net for all windows and plastic curtains for door exit. 2. Insect killer light is installed. – No animals around factories. 3. Doors/windows are locked by shift end. 4. All unseal cartons/products are sealed/covered before factory closed. 5. Separate de-humidifying room with temp 20°C and <55% humidity control with record and racks are used for humid seasons. Install thermometer and hydrometer for record. 6. Check product humidity in final inspection by Aqua boy meter. 7. All windows are installed with window screen. 8. Gauze net should be installed on the external openings, air-vents on the roof, and exhaust fans. 9. All external doors are installed with gauge curtain. 10. Cover all finished/semi-products at packing area. 11. Install rat guard in all production area. |
04 Pressing – Finishing – Packing | Same as 3 while – For high risk humid countries, air conditioning with humidity control. – If not high risk humid countries, a good ventilated room with humidity indicator is acceptable. Clean and tidy. High risk countries: Cambodia, Vietnam, Indonesia, Malaysia, Myanmar, Bangladesh, South China. |
04 Pressing – Finishing – Packing | Found any garment getting dirt / stains from environment. or >20% pressed garment under improper storage. |
04 Pressing – Finishing – Packing | Very dirty environment. Many garments need to be washed or cleaned before packing. |
05 Inspection | 1.Does factory has a complete set of their buyer’s technical manual hard copy/ approved samples provided to each QA and knows how to obtain updated information? |
05 Inspection | -Factory has a complete set of their buyer’s technical manual hard copy -Approved samples are provided to each QA. -QAs have access to obtain updated information with translations when needed. |
05 Inspection | -Factory has a complete set of their buyer’s technical manual hard copy. -Approved samples are shared between production and QA. |
05 Inspection | -Their buyer’s technical manual hard copy is incomplete or outdated – Only some approved samples are provided to QA. -QAs do not know how to obtain updated information. |
05 Inspection | -Factory does not have their buyer’s technical manual hard copy. -Most of approved samples cannot be access by QA. |
05 Inspection | 2.Has the factory an independent QA/QC team? Check the organization chart. |
05 Inspection | -All roving/inline/end line QA/QC team in all sections is independent. They are not reported to the production. Factory has a clear organization chart. |
05 Inspection | Only the finishing section end line inspection QC and AQL shipment QA/DA are independent from the production team. |
05 Inspection | Only AQL shipment QA/DA teams is independent from the production. |
05 Inspection | -Factory does not have clear inline/end line QA/QC team; trimming and QC is same person; or all QA team are reporting to the production head. |
05 Inspection | 3.For subcontracted semi-products/parts/ plating, is there a complete and clear standard provided and if there is any QC station there to monitor? |
05 Inspection | -Factory has hold PPM with sub-contracted with a record. – There is a clear instruction & SOP of every item for sub-contractor semi-products. – There is QC stationed in subcon daily and sends inline/ end line report for subcon product delivered. |
05 Inspection | -Factory has a clear instruction & SOP. – factory sends QC to check pilot /1st bulk but not stays till all bulk finished. – There is a completely checking upon receipt for all sub-con materials. |
05 Inspection | Either there is insufficient instruction for subcon or not enough QC coverage (i.e. either no sending QC / not completely checking upon receipt) to ensure bulk consistency. |
05 Inspection | There is no QC report/ no checking before subcon products flow to production. |
05 Inspection | 4.Are there checking in a daily basis to ensure correct machine setting (sip and check seam stretch ability) with record? |
05 Inspection | There is clear spec sheet per sewing station with sip and seam stretch checking cloth that operation checked and passed before bulk production starts everyday. |
05 Inspection | same as the Good rating but it is checked by supervisor or QC. |
05 Inspection | there is insufficient data in the spec sheet or incomplete checking cloth result found. |
05 Inspection | no such setting. |
05 Inspection | 5.Is there a proper training for QA/QC and to develop their ability to cover multi-departments (roving/ inline/ end line inspection)? |
05 Inspection | -There is a good and systematical training for a new QA/QC. -Good management planning and enough manpower planning of QA/QCs, for Gap, to work in multi-departments. – QA & QC have passed Munsell eye test with error score 20 or below. |
05 Inspection | -There is a good training for a new QA/QC. – QA & QC have passed color blind test by color book. |
05 Inspection | -Insufficient training provided for a new QA/QC. -Insufficient QC – no flexibility to swap QC between departments. – some QA & QC do not pass color blind test |
05 Inspection | -No training provided to a new QA/QC. -No back up plan to replace in the absence of QA/QC. – no color blind test |
05 Inspection | 6. Randomly select one style from the finished goods in WIP to check if 100% inspection is applied. |
05 Inspection | -There is end line QC per sewing line/ section. – Randomly review some QC checked products, found their rejected / passed are valid. – check 5 pcs from one station and pass/reject pcs are aligned. – Has a clear reference sample and Tech Pack available per station. – QC report is clear with defect type %. – End line QC completely checks all bulk for visual defects and around 20% for critical measurement. |
05 Inspection | There are 100% visual inspection but random daily POM inspection. |
05 Inspection | Found 1 pc defects out of 5 pcs of checked garment. or any missing info or mistakes done by QC. |
05 Inspection | Found > 2 pcs of defect or no 100% inspection process. |
05 Inspection | 7.Is lighting adequate and enough space with completed information and acceptable temperature & humidity in QC room/QC stations ? |
05 Inspection | -Lighting is adequate (800-1000 for apparel and 600-800 for non-apparel) lux and space is enough in all inspection station from warehouse to finishing. -There is a complete information, quality standard, approval sample, at shading / QC stations. air con available in QC room to control temp and humidity. |
05 Inspection | -Lighting is adequate and space is barely enough for table and inspection. cartons needs to put outside the room. -There is complete information but not for their own, they need to share information with other production departments. |
05 Inspection | -Lighting is out of desire range or space is not enough to have 2-3 QC working in same room. -Information is incomplete at QC stations. |
05 Inspection | There is no QC room, QC station is at open space area next to production stations. |
05 Inspection | 8. Does factory conduct 100% lamp checking after laundry & before pressing? |
05 Inspection | 100% before and after washing |
05 Inspection | 100% after washing |
05 Inspection | less than 100% |
05 Inspection | no light tube |
05 Inspection | 9. Regarding the inspection combined with this TE/PA, is the inspection result Pass or Fail? |
05 Inspection | pass brand AQL |
05 Inspection | failed brand AQL |
06 Product Safety | 1.Is metal control efficiently done in sample room, the whole production floor and QC room ? |
06 Product Safety | – No metal staples, pins and wires used in any part of the production process for bundling, tacking, sewing, packaging or securing components; it is verified that the Metal Tool Control Log (incl. scissors, razors, clippers, hand-sewing / embroidery needle, replacement needles for Kimball tag guns) is being monitored. – If pins must be used in specific garment manufacturing process, such as fabric laying and cutting, the factory is requested to maintain the documented record for the control of pins. – Records must be kept minimum one year on site. – Any suspicious broken needle missing, all products should undergo scanning to identify or disposal if cannot find. |
06 Product Safety | found non-conformance part as per the listed policy. |
06 Product Safety | 2.Are metal tools and hard tags in the Metal Free Zone in packing area under proper control and Metal Free Zone is free from unauthorized entry ? |
06 Product Safety | – Metal free zone is properly controlled with limited authorizes person to enter. Entry always keep close and arranged security check for the in & out person with record. – All the authorizes persons are with a permit to enter the metal free zone. ‘- all hard tag are proper control with record. |
06 Product Safety | There is no metal-free zone or found non-conformance part as per the listed policy. |
06 Product Safety | 3.Does Needle Detector function consistently and 9-point calibration and relevant record keeping are completed 3 times per shift? (1.2 mm sensitivity) |
06 Product Safety | – Needle Detector functions correctly (1.2 mm sensitivity) and 9 point calibration is performed correctly with complete record. – Calibration is done for more than 3 times per shift. – Well maintenance by needle detector supplier with valid record. – Recalibration is not expired. – Needle Detector in GSS listed brand. |
06 Product Safety | There is no needle detector or fails in calibration. |
06 Product Safety | 4.Are all needle control and detection logs done, verified and retained properly ? |
06 Product Safety | – No broken needle parts are found in production areas. Record every needle breakage and be completed at the time of the occurrence, allocate all parts of the needle and securely mounted to the log for each entry, maintain clear records for 1 year. – If part of needle fragment cannot be found after the intensive search, the operator must clearly report the follow-up action and date/time of needle detection for broken needle in the broken needle log. |
06 Product Safety | There is no needle control process or found non-conformance part as per the listed policy. |
06 Product Safety | 5.For Machine-Attached Hardware (MAH) applied on Kids/Baby products, is Garment Check & Recommendation (GCR) Datasheet issued by MAH Supplier per style and reviewed in the PP meeting ? |
06 Product Safety | – GCR Datasheet is issued by Gap Inc. Qualified Kids/Baby Trim Supplier. – GCR Datasheet is issued before production. – GCR Datasheet is issued for every Kids/Baby style (unless the style is carry-over) – GCR Datasheet is concluded as “APPROVE” – GCR Datasheet is downloaded from Vendor headquarter to Factory and Factory reviews during PP meeting. – GCR Datasheet is ready in production floor for operator’s usage to check machine pinch setting. – A person or team is assigned to follow up the GCR Datasheet from receipt from MAH Supplier, booking supplier’s technician for machine setting, a copy filed in MRP to retaining e-copy for 12 years. |
06 Product Safety | There is no GCR Datasheet or found non-conformance part as per the listed policy. |
06 Product Safety | 6.Is there regular checking and maintenance of the die molds and attaching machines used for MAH trims ? |
06 Product Safety | – Ensure regular machine maintenance from MAH Supplier. Actively call out if not happening. – Do not use damaged die molds. Do not keep or re-use damaged die molds. – Must use same attaching machine, die mold, MAH trim from the same MAH Supplier for Baby products. – Attaching machines must be semi-automatic or fully automatic pneumatic / electric presses. – Keep records of the die molds and attaching machines for monitoring. |
06 Product Safety | found non-conformance part as per the listed policy. |
06 Product Safety | 7.Are MAH control logs at PP, inline daily shift, 100% inspection done, verified and retained properly ? |
06 Product Safety | – 50 sets or pcs of mock-up in correct quality are checked for attachment strength, 5 sets or pcs checked for pinch setting at PP stage. – 5 sets or pcs of mock-up in correct quality are checked for attachment strength, 1 set or pc checked for pinch setting at inline daily shift. – For Baby style with snaps attached: Factory uses Saf-Q to test bulk garments for Attachment Strength and Unsnapping per style at each stage of production (beginning, middle, end). – 100% physical and visual inspection done immediately after attachment. – Correct templates (Form 1, 2, 3, 4 as specified at PSR SOP 010) are used. Provide with local languages for translation is acceptable. – Retain hard copies of the Control Logs (Form 1, 2, 3, 4) for 1 year. – More often inline checking than required. |
06 Product Safety | found non-conformance part as per the listed policy. |
06 Product Safety | 8.For Baby production, does new MAH attachment operator receive training from MAH Supplier ? |
06 Product Safety | – Notify MAH Supplier to arrange on-site training to new hired attachment operators. – Hold regular training to factory operators, QC inspectors. – Keep training records of each attachment operator, QC inspector. |
06 Product Safety | found non-conformance part as per the listed policy. |
06 Product Safety | 9.For MAH applied on Kids/Baby products, does factory own Saf-Q attachment strength tester and operator is able to perform testing per Gap Inc. Test Method S-2001 ? |
06 Product Safety | – Factory own Saf-Q tester. – Operator understands and performs MAH Attachment Strength and Unsnapping testing correctly. – Factory use correct clamping devices for Attachment Strength and Unsnapping tests (specified at TM S-2001). – Factory know to pull bulk products (with ring prong snaps or any styles identified as high risk and Expedited Attachment Strength test is needed) from different attaching machines and submit to Lab for Expedited Attachment Strength test once production starts. |
06 Product Safety | There is no SafQ tester or found non-conformance part as per the listed policy. |
06 Product Safety | 10.Is there Lock Stitch button attachment machines? |
06 Product Safety | Yes. There is Gap required machines. |
06 Product Safety | No. For new factories, put in remark to mention if factory is willing to buy or not upon order. |
06 Product Safety | 11.Is Button Control Procedure checked, verified and maintained the records properly? |
06 Product Safety | – Stitch pattern is complete and in tidy, clear-cut thread-ends and cross-stitch shape, which is also adjusted to fit in the button line size and design – No discrepancy is found in attached buttons and observes the button check procedure in place – Operator always checks the evenness of thread tension and record the details in daily records ‘- All important information is properly recorded and filed, such as date, time, output, failure nature and correction made, etc. |
06 Product Safety | found non-conformance part as per the listed policy. |
06 Product Safety | 12.For Kids/Baby production, does factory have Approved Safety Line Review Reports downloaded from Safety Line Review Focals (SLRF) and gone through in PP meeting ? (N/A for new factory) |
06 Product Safety | – the vendor has empowered Safety Line Review Focal (SLRF) recognized by Gap Inc. – the Safety Line Review Report is signed off by SLRF, filed at MRP. – additional control set by factory on top of Gap Inc. SOP. |
06 Product Safety | found non-conformance part as per the listed policy. |
07 Sample Making Room | 1.Are there design technician support prompt sample making with buyer specification? |
07 Sample Making Room | – There are qualified pattern makers / production designer technician / sample maker assigned per brand on site. – Pattern making / adjustment / corrections range is 1/2 of the tolerance for bulk pattern. – All patterns are verified and signed. |
07 Sample Making Room | – There are qualified pattern makers while there is no assigned per brand. – Pattern making is 1-2 days per style. – Pattern making / adjustment / corrections range is the total tolerance for bulk pattern. – All patterns are verified and signed. |
07 Sample Making Room | The current pattern maker is not knowledgeable of similar GAP styles. Or there is insufficient pattern maker. ‘- Pattern making / adjustment / corrections range is more than total tolerance for bulk pattern. |
07 Sample Making Room | There is no pattern maker on site. All patterns are made in vendor sample room. No technical support for pattern adjustment. |
07 Sample Making Room | 2.Is there a sample development process to evaluate production capability against customer requirements prior to order commitment? |
07 Sample Making Room | There is a process to involve sample technician and production supervisor during sample development to sign off the sample construction that can be consistence in bulk production. Actual bulk production template and machine setting are designed during sample development. Factory use the highest quality level among their buyers for all brands and give options to buyer. |
07 Sample Making Room | Same as Good rating while factory starts involvement upon order confirmation. |
07 Sample Making Room | There is insufficient communicate between sample technician and production or insufficient understanding of the sample room technician on their buyer’s requirement. |
07 Sample Making Room | There is no indication or document or process to show |
07 Sample Making Room | 3.Is there a procedure in which key product requirements, though missed by the customer, are determined and communicated? |
07 Sample Making Room | There is a library of constructions as per final use of product. Factory conduct functional test to ensure the key product requirement. Any non-compliance features are corrected before sample submission. |
07 Sample Making Room | Factory conduct functional test as Good rating but factory did not have a library of construction to follow. Therefore, they rely on their experience technician to correct non-compliance features. |
07 Sample Making Room | There is insufficient functional test so risk in non-compliance features. |
07 Sample Making Room | Factory follows buyer’s request without any verification. |
07 Sample Making Room | 4.Is there a process to ensure that design and development changes are verified, approved, communicated and executed? |
07 Sample Making Room | For each changes, there is involved of process in Q2 and Q3 to ensure product qualified to end use. |
07 Sample Making Room | Factory only checks in the initial stages and before sample adoption. There is no checking as per each changes. |
07 Sample Making Room | There is insufficient checking before sample adoption. |
07 Sample Making Room | Factory follows buyer’s request without any verification. |
07 Sample Making Room | 5.Is the sample room fully equipped with proper machines in good condition to produce approved samples that are representative of factory’s specific product types? |
07 Sample Making Room | – Sample room is well organized. – Sample room is fully equipped including cutting equipment and table, fusing machine, sewing machines of all types, including finishing machines (button, buttonhole, snap), pressing equipment, working aids, needle gauge, attachments, forms, computerized grading system; computer art work (sweater); dimension design system; all kinds of machineries for hardware product as needed for Gap Inc styles. All machines are in good condition and plotter calibrated. |
07 Sample Making Room | – sample room has same setting as Good rating. Just missing some sub-con machines like embroidery, printing. |
07 Sample Making Room | – sample room did not equip with same set of machinery as in production. |
07 Sample Making Room | – No sample room |
07 Sample Making Room | 6.Are there mannequins / complete GSS latest mannequins? |
07 Sample Making Room | – There are correct latest mannequins for all Gap Inc. brands. – There are well designed functional testing forms / jag & fixtures / mold. |
07 Sample Making Room | -There are mannequins for other brands or duplicated copies. – There are functional testing forms / jag & fixtures / mold. For new factory, if factory agree to buy upon order placement, put it at overall comment and this will put as a condition under approval letter. |
07 Sample Making Room | – There are missing or broken mannequins |
07 Sample Making Room | -There is no mannequins / forms / jag & fixture / mold |
07 Sample Making Room | 7.Is computerized pattern system with regular calibration? E.g. apparel: CAD system/ with record of last 2 years style. |
07 Sample Making Room | There is a computerized system to record more than last 2 years of data. – the pattern plotter is regularly calibrated. |
07 Sample Making Room | There is a computerized system with record of only last 1 year’s data. – no calibration record but the current plotter patterns are in good quality |
07 Sample Making Room | There is a printer only, no computer to change / adjust pattern. The record is only current production. |
07 Sample Making Room | Not using any computer system. |
07 Sample Making Room | 8.Is there detail production specification for production floor to follow. For example: prewash measurement, heat set / washing temperature, drying temperature, construction/assembly? |
07 Sample Making Room | – There is detail production specification with mock up or buyer’s approval comments or sample room comments or pilot run comments stacked on the approval sample with name, signature and date for the production floor to follow. – All the comments including buyer’s are also attached with the approval sample. |
07 Sample Making Room | – There is detail production specification/buyer’s approval comments/sample room comments/pilot run comments stacked on the approval sample with name, signature and date for the production floor to follow. – buyer comments are transferred at local language |
07 Sample Making Room | – There is insufficient production specification/buyer’s approval comments/sample room comments/pilot run comments attached with the approval sample. |
07 Sample Making Room | There is no production specification or wrong info passed to the production. |
07 Sample Making Room | 9.Are fabric, trims and parts well organized in sample room? Is house keeping acceptable? |
07 Sample Making Room | -Sample fabric, trims & parts are well organized by buyer/ item/ style number. – Good and clean storage racks. |
07 Sample Making Room | – Sample fabric, trims & parts are fairly organized but not separated by buyer. – Place is clean and acceptable. |
07 Sample Making Room | – Need to improve storage of fabric, trims and parts. – Need improvement in cleaning and organize. |
07 Sample Making Room | Dirty and not organized places. |
08 Lab | 1.Are there in-house lab tests performed in order to control bulk material consistency? |
08 Lab | Full scope of test per category + technician was trained and certified by third party + inhouse lab was accredited by third party or GSS for basic test+ can perform FGs test (not only materials) + clear testing plan and procedure |
08 Lab | Consisted equipment of those “must have” tests listed + technician was trained by third party + inhouse lab was approved by GSS PI OR lab meet requirement of correlation program + clear testing plan and SOP |
08 Lab | Insufficient test or testing personnel / equipment setting. |
08 Lab | no testing conducted. |
08 Lab | 2.What is the sampling size for raw material/ trims test conducted per style in-house lab? |
08 Lab | Factory had clear testing plan with sample size and acceptance, requirement for all materials/trims – daily or weekly bulk batch testing. |
08 Lab | Factory had testing plan with sample size and acceptance, requirement for main materials and few trim only. Testing per style per season. |
08 Lab | Insufficient test or sample size. |
08 Lab | no testing conducted. |
08 Lab | 3.Is there an organized testing report keeping? |
08 Lab | Records are well kept for each material for 1 year period. |
08 Lab | Records are well kept for each material for minimum 6 month period. |
08 Lab | There was insufficient reports or report keeping less than 6 months. |
08 Lab | No report, no indication of material bulk testing control. |
09 PP meeting | 1.Is there a completed MRP / QC file for each style? |
09 PP meeting | The info below is found in MRP: 1. Purchase Order/DPO 2. Tech Pack or technical specification for accessories 3. Fabric/Garment Test Report for apparel, Product Test Report for accessories) 4. Buyer final comment 5. GAP approved sample/ mock up 6. Approved Trim card <5-6 needs GSS VM/ Vendor merchant / VKR/FKR stamp/ signature> |
09 PP meeting | Same as Good Rating while items 5-6 have email only, no signature. |
09 PP meeting | Any 1-2 items missing from Good rating. |
09 PP meeting | No QC file. |
09 PP meeting | 2.Does Quality manager follow PPM Guideline effectively and record in PPM report? (such as who attend PPM, critical operation, safety….etc.) |
09 PP meeting | Quality manager follows for key style/ high risk style extensively and setting critical operations and assign QC. All PPM report done by FKR. Quality manager. |
09 PP meeting | Quality manager follow all styles as per PPM Guideline, clear PPM report and all dept. supervisor follow with report on site. |
09 PP meeting | Quality manager role in PPM is insufficient. |
09 PP meeting | Quality manager did not aware PPM guideline. |
09 PP meeting | 3.Is size set sample per color way prepared and reviewed according to measurement, visual, fitting, testing and related performance test with report for bulk adjustment? |
09 PP meeting | – Full/Jump size set sample in combine color <include all colors> is prepared and reviewed according to measurement, visual, fitting, testing and related performance test with report for bulk adjustment. |
09 PP meeting | – Jump size set in selected colors <not all colors> is prepared and reviewed according to measure, visual, fitting, testing and related performance test with report for bulk adjustment. |
09 PP meeting | – S/M/L set in one color way is prepared and reviewed according to measure, visual, fitting, testing and related performance test with report for bulk adjustment. |
09 PP meeting | – Only 1 size is prepared and reviewed according to measure, visual, fitting, testing and related performance test with report for bulk adjustment. |
10 Management | 1.Is there a computerized system to access reports highlighting production output and efficiencies, quality control performance, order status and other essential and helpful data to properly manage factory operations? |
10 Management | -Review the system which can show style level daily output and quality performance is clear enough for root cause analysis. |
10 Management | – The system can only be reviewed on a weekly basis so the reaction to a problem is slow but still can react to avoid delivery delay. – daily manual report are inputted into computer for analysis. |
10 Management | – All the systems are hand written, which does not allow managers to make decision and follow up on time. |
10 Management | – There is limited manual system which does not allow managers to make correction to prevent delivery delay when quality issues/output issues. |
10 Management | 2.Is there an internal system to work with their suppliers on evaluation the material quality performance and pro-actively work out to prevent raw material/trim/ semi-product quality issues? |
10 Management | – There is system to show the trim/fabric supplier performance and ranking and regular score card/ meetings conducted to request for improvement |
10 Management | – There is raw data in electronic database available to draw the data when factory wants to have a performance improvement from supplier. 80% of supplier are covered. |
10 Management | Insufficient data or less than 80% supplier has record. |
10 Management | -There is limited paper inspection reports which needs a lot of time to generate supplier scorecard. |
10 Management | 3.Is the quality mind set of the factory management staff and their reaction when there is a CAP / suggestions during the visit appropriate? |
10 Management | – Found all staffs are very proactive/ motivated/ take quick action when reacting to CAP/suggestions during visit. They can fully demonstrate commitment with resources and concrete timeline. Clear SOP of CAP provided. FKR uses QC 7 tools or IE approaches to solve issues. |
10 Management | – Found only middle/ top management are proactive/ motivated/ quick when react to CAP/suggestions during visit. |
10 Management | Only the FKR is proactive while found FKR is incapable to execute the changes. |
10 Management | Found all staff are very passive/slow/negative to react to CAP/suggestions during visit. |
10 Management | 4.Are there procedures in place to measure and analyze process, product quality data including analysis of long-term trends? |
10 Management | There is clear SOP with report of last 3 months shown. Factory should implement this for min 1 year. There should be improvement shown in the performance trend chart. |
10 Management | Same as Good rating while this is implemented start in last 3 months. |
10 Management | There is either no improvement in the performance trend chart or the SOP is incomplete implemented so the supervisor is not using the data to improve. |
10 Management | No procedure. No record. |
10 Management | 5.Are the results of preventive or corrective actions reviewed by top management and used to improve the Quality and Product Safety management System? |
10 Management | There is clear SOP that there is appointed IE/QA person consistently review the performance report and keep upgrade their QM system to improve. There should be improvement shown in the performance trend chart. |
10 Management | Same as Good rating while the CAP demonstrated are within 1 year period. None is done in current 3 months. |
10 Management | Factory only perform CAP as per customer request. |
10 Management | no CAP record found. |
11 Hiring & Training | 1.Is there a proper hiring program so relative product experience and English proficiency are included? |
11 Hiring & Training | Clear record, factory can demonstrate how they do it. |
11 Hiring & Training | with some record and factory can demonstrate how they do it. |
11 Hiring & Training | Clear record but factory cannot demonstrate how they do it. |
11 Hiring & Training | no record and factory cannot demonstrate how they do it. |
11 Hiring & Training | 2.Is there a proper training program for new hires before they can work independently? |
11 Hiring & Training | Clear record, factory can demonstrate how they do it. |
11 Hiring & Training | with some record and factory can demonstrate how they do it. |
11 Hiring & Training | Clear record but factory cannot demonstrate how they do it. |
11 Hiring & Training | no record and factory cannot demonstrate how they do it. |
11 Hiring & Training | 3.Are there goals and incentives for all operators to improve quality, product safety, efficiency? |
11 Hiring & Training | There is operators output/defect % record in real time with display per operator for the incentive plan. The reaction of operators toward the supervisor correction action are all very positive. |
11 Hiring & Training | same as Good rating while the output/defect % capture is in a white board in front of the sewing section. There is no individual person data, only data per sewing line. |
11 Hiring & Training | Factory show some proof for the incentive plan while there is no output/defect % capture on site. Or the operator is not very positive on changes/corrections. |
11 Hiring & Training | Operators are negative or ignore all the corrections / changes. |
11 Hiring & Training | 4.Is there any policy and incentives to reduce the undesired turnover rate? |
11 Hiring & Training | There is attractive policy and incentives so that undesired turnover rate is less than 5% |
11 Hiring & Training | Same as Good rating while the turnover rate is 5-10%. |
11 Hiring & Training | not enough incentive so the turnover rate is 10-20%. |
11 Hiring & Training | no incentives at all. Turnover rate over 20%. |
11 Hiring & Training | 5.Is there a regular performance review with improvement plans for staff so they can keep upgrading in their skills? |
11 Hiring & Training | There is a regular performance review ( every 3 months or less than 3 months) with improvement plan |
11 Hiring & Training | There is a regular performance review ( longer than per quarter while at least per year with improvement plan |
11 Hiring & Training | There is no regular performance review, only supervisor identify any staff who needs improvement. |
11 Hiring & Training | no performance review. |
12 Laundry | 1.Is laundry managed by qualified technician / chemist? |
12 Laundry | – Facility has qualified technician / chemist to provide washing formula. – They also do research & development. – Test the water quality regularly to ensure consistency. |
12 Laundry | – Laundry house has experienced wash technician but no chemist. – Not strong in research and development. |
12 Laundry | either technician / chemist does not conduct the tasks consistantly. |
12 Laundry | – There is no qualified technician / chemist. |
12 Laundry | 2. Are laundry formulas, buyer approved samples for shade/hand feel & Tech Pack readily available for operators’ and inspector’s easy reference? |
12 Laundry | – There are laundry formulas, buyer approved samples for shade/hand feel & Tech Pack (all the information are verified by QC, with name, signature, date) readily available for operators’ and inspector’s easy reference – For the bulk consistency, laundry supervisor should have a pre-production meeting with workers to ensure their understanding on buyer requirement – Create copy of the original approved samples with signature & date and keep them at laundry; and change the copy every three days; and original sample should be kept in dark bag. |
12 Laundry | There are laundry formulas, buyer approved samples for shade/hand feel & Tech Pack readily available for operators’ and inspector’s easy reference – did not put the original buyer sample in dark bag, put it at laundry while have an update one per season. |
12 Laundry | There are unclear laundry formulas, buyer approved samples for shade/hand feel & Tech Pack. Are not readily available for operators’ and inspector’s easy reference – the buyer approved sample is not properly kept and looks deteriorated. |
12 Laundry | There are no laundry formulas, buyer approved samples for shade/hand feel & Tack Pack readily available for operators’ and inspector’s easy reference |
12 Laundry | 3. Are machines adequately maintained with no steam/water leakage, no rusting or broken parts? |
12 Laundry | – All machines are in good condition with adequately maintained for bulk execution -All meter and valves are checked and no leakage. – With clear record or log book mark the date of maintenance |
12 Laundry | Same as 3. – But some machines have no maintenance record shown. – Working condition not as good as 3. |
12 Laundry | -Only part of machines are adequately maintained for bulk execution with incomplete or unclear record. – Working condition need further improvement. |
12 Laundry | -Machines are in poor condition & not adequately maintained. |
12 Laundry | 4. Is there checking of machine temp and RPM recorded? Is there infra red temperature indicators for the dryers and DataPaq temperature checking device for Ovens available? |
12 Laundry | -There is 2 checking per day of all machine temp and RPM with clear record or log book posted to every machine -There is infra red temperature and Databa temperature checking device on site. |
12 Laundry | Same as 3 while checking is once per day. |
12 Laundry | There is a regular checking of some machine temp and RPM but incomplete record -The infra red temperature and Datapaq temperature checking device is available but not functioning well in facility |
12 Laundry | No checking device and no checking for temp and RPM. |
12 Laundry | 5.Any calibrating measuring devices used? E.g. weight, beaker |
12 Laundry | -There are sufficient calibrated measuring device used and calibrated in 6 months period with current update record |
12 Laundry | Same as 3 while calibrate in yearly basis. |
12 Laundry | -There are insufficient calibrated measuring device used -Calibration records are not clear or not properly filed or less frequent than acceptable |
12 Laundry | -There are no calibrated measuring device used |
12 Laundry | 6. Are measurement and hand feel checked and recorded per machine load? |
12 Laundry | -There are measurement and hand feel checking by reviewing few pieces per machine load with clear record. -Measurement checkers perform correctly on measuring method -With approval hand feel standard for checking -Assigned person are responsible to analyze measurement performance and hand feel so as to take immediate corrective action. |
12 Laundry | Same as 3 while no assigned person responsible for measurement performance analysis and hand feel standard |
12 Laundry | – Measurement and hand feel are checked by reviewing few pc per style. – Some checking procedures are not sufficient. |
12 Laundry | No checking. Very serious issues found in current approved to delivery bulk garments. |
12 Laundry | 7.Is there light box with buyer required light source available? Any qualified colorist ? (n/a if covered under lab section) |
12 Laundry | – – Buyer approved shade, hand feel, color band, are available and referred during inspection. – Inspectors are well trained and had taken color blind test. – Inspection work station desire light intensity is 800-1000 lux for apparel and 600-800 for non-apparel. Gap approved light box used. |
12 Laundry | -same as Good rating, while the light box is same light source as Gap require. For new factories, if factory agreed to buy upon order placement, mark in TE report comment as condition for approval. |
12 Laundry | – any insufficient points listed in Good rating is needed. Light at inspection work station is out of desire range. |
12 Laundry | No fabric inspection conducted or no report. |
12 Laundry | 8. Is the laundry workshop clean & in good condition? |
12 Laundry | – The entire workshop is neat, clean and well ventilation. With no water stagnation. – All the chemical materials with secondary container have been stored in a well organized and separated area with MSDS sheet. – All the chemical containers/ flask on production floors have clear labels and warning. – All the tables and storage racks and cabinet are clean. |
12 Laundry | Same as 3 while some workers do not follow MSDS/SOP strictly. |
12 Laundry | >20% deviation from Good Practice and low risk in defects. |
12 Laundry | – Materials do not store in a separate area for chemicals. – No workers have been trained to follow the SOP. |
13 Embroidery | 1.Are buyer’s approved samples/Tech Pack/trim cards provided as guides for operators? |
13 Embroidery | Buyer’s approved samples/Tech Pack/trim cards are provided in the production floor/line. |
13 Embroidery | Buyer’s approved samples/Tech Pack/trim cards are provided in the production supervisor’s desk. |
13 Embroidery | Some of the supporting documents are incomplete. |
13 Embroidery | >50 styles have incomplete approval sample / tech pack / trim cards |
13 Embroidery | 2.Are embroidery machines properly maintained, regularly cleaned and serviced, and in good condition? |
13 Embroidery | All machines are in good condition and clear maintenance record displayed per machine. |
13 Embroidery | All machines are in good condition but the maintenance record are in the mechanic’s log book. |
13 Embroidery | No clear/ incomplete maintenance record. Found some machines in poor conditions. |
13 Embroidery | No maintenance record, most machines found in poor condition. |
13 Embroidery | 3.Does the embroidery facility have a broken needle control process and are all outgoing panels checked? |
13 Embroidery | 1/Product Safety Officer (PSO) executes Gap product safety procedure in factory. 2/Needle keeper executes Gap control broken needle procedure in factory. 3/Factory checks all embroidery semi-pieces by Gap certified needle detector before delivers to garment factory. |
13 Embroidery | Point 1 & 2 as “Good Rating”, but bulk is checked and scanned at garment factory |
13 Embroidery | Same as “Good Rating” while there are some stations with Partial compliance to GAP requirement |
13 Embroidery | No PSO or insufficient PSO checking. No record to show needle detection on all panels. |
13 Embroidery | 4.Is thread SPI/tension well monitored and controlled, and thread ends properly trimmed? |
13 Embroidery | – There is daily SPI/tension checking per machine according to design/fabric/thread. – All thread ends are trimmed by auto trimmer at machine or manual QC station with <1/8 left. |
13 Embroidery | 80% or above machines are well monitored and controlled. And thread ends defect is <20%. |
13 Embroidery | 20% or above machine not set up properly and 20% or above thread ends defects. |
13 Embroidery | 50% or above machine not set up properly and50% or above thread ends defects. |
13 Embroidery | 5.Is there a complete visual checking and separate packing per shade in enough lighting when needed? |
13 Embroidery | There is 100% visual checking and clearly labelled per panel – Desire lighting intensity is 800-1000 lux for apparel and 600-800 for non-apparel. |
13 Embroidery | There is 100% visual checking and only labelled per bundle. |
13 Embroidery | Random visual checking and labelled per bag. – lighting intensity is out of the desire range mentioned in “Good rating”. |
13 Embroidery | No visual checking or no label used to separate shading. |
13 Embroidery | 6.Are there in-process and finished pieces inspected and seconds replaced before releasing back to production workflow? Are there proper control of deviations per load? |
13 Embroidery | – Buyer approved detail information available for QC. – Check by AQL sampling with clear QC report per load. – There is a clear separation of seconds and return back to rectify by batch/load. – Bulk rectified before sending back to production. |
13 Embroidery | Technical Audit Checklist in Sweater- Same as “Good Rating” while checking and rectifying in daily basis. |
13 Embroidery | Same as “Good Rating” while some pieces/ stylings are not follow properly. |
13 Embroidery | no QC report. Only rectify till next section or finishing QC rejected. |
Conclusion
A neutral auditor can do a periodic audit to check according to Technical Audit Checklist in the Sweater Industry. Report from him give management a signal.
- You may love to read: Technical Audit Checklist of the Garments Industry
- Technical/ QMS/ Quality Audit Checklist of Footwear Industry