Elevating Fabric Inspection with Quality 4.0 in Textile and Apparel Industry
Rapid technological innovation is causing sectors all over the world to undergo radical change, and the textile sector is no different. Modern technologies are introduced by Quality 4.0, a development of traditional quality management, to improve productivity, accuracy, and efficiency. Fabric inspection is one crucial area where Quality 4.0 is creating waves, transforming the way textiles are evaluated for compliance and quality.
Understanding Quality 4.0
The term “Quality 4.0” refers to the process of incorporating digital technologies into quality management procedures. It uses advanced technologies like machine learning, big data analytics, artificial intelligence (AI), and the Internet of Things (IoT) to increase overall product quality and streamline operations. Quality 4.0 offers a thorough and data-driven approach to fabric inspection, extending beyond traditional methods of inspection.
Key Differences Between Traditional Quality Systems and Quality 4.0:
Aspect | Traditional Quality Systems | Quality 4.0 |
Technology Integration | Manual processes, basic computer tools | Advanced tech like IoT, AI, and sensors |
Data and Analytics | Manual data collection, limited analytics | Real-time data, advanced analytics |
Interconnectivity | Siloed operations, limited communication | Seamless connectivity across processes |
Risk Management | Reactive risk management | Proactive risk identification and prevention |
Customer Focus | Customer feedback collected but not well integrated | Strong emphasis on customer feedback and integration |
Agility and Flexibility | Often rigid and slow to adapt | Agile and flexible to adapt quickly |
Traditional Systems use simpler tools and manual processes, while Quality 4.0 uses fancy technology like smart sensors and computers that talk to each other. Quality 4.0 is smarter, faster, and cares a lot about what customers think. It’s like comparing an old bicycle to a new, high-tech electric scooter!
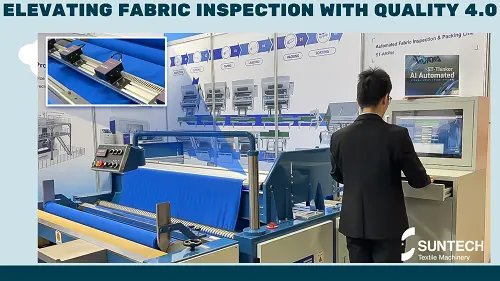
Why Quality 4.0 in Fabric Inspection
Using Quality 4.0 in fabric inspection is like upgrading to a smarter system. Sometimes, small fabric problems are missed by people, leading to money loss in subsequent steps like dyeing and sewing. A Fabric Scanner catches these issues fast, so we can fix them quickly. This helps us save money by avoiding making garments with problems. Quality 4.0 makes everything work better, saving costs and making sure our final products are top-notch. It’s like a smart upgrade for better control and great results in making garments. Also it will reduces manpower expenses in fabric inspection. In a medium-sized knit factory with 1000 machines, the Fabric Inspection Department, consisting of 15-20 manpower working in two shifts, oversees visual inspection, shade assessment, and lab testing to ensure the quality of fabrics and rolls movement.
However, with the integration of Quality 4.0, there will be a substantial reduction in manpower requirements. The fabric inspection department can be efficiently managed by a sole incharge, leading to decreased manpower costs while ensuring a high-quality inspection system.
Key features of Quality 4.0 in fabric inspection
- Automated faults detection: The heart of AI-powered fabric inspection lies in the deployment of high-resolution industrial cameras that are equipped with advanced AI algorithms. These smart machines can automatically pinpoint and highlight defective areas in the fabric. Automated fault detection not only speeds up the inspection process but also guarantees a level of precision that outperforms conventional methods.
- Dynamic Machine Intervention: When smart machines find a problem in the fabric, they can quickly stop working. This helps make sure that no more mistakes happen, and it marks the spot where the problem is. This is useful for two reasons. First, it stops bad products from being made. Second, it lets people check the fabric again by hand if needed. The human touch can easily be added to the automated process, making sure the quality is even better.
- Real-time monitoring and smart sensors: Quality 4.0 makes use of advanced smart sensors integrated into the fabric inspection procedure. These sensors gather data in real-time and continuously, making it possible to carefully examine each fabric attribute. The fast discovery of problems is ensured via real-time monitoring, which enables timely corrective actions. The machines generate a real-time display of various crucial metrics, offering a comprehensive overview of the inspection process. Some of the key parameters include:
- Defect Distribution Map: Visual representation of the distribution of defects across the fabric.
- Defect Detailed Information: In-depth insights into the nature and characteristics of detected defects.
- Real-Time Fabric Width: Continuous monitoring of the fabric width during inspection.
- Fabric Inspection Speed: Live updates on the speed at which the fabric is being inspected.
- Length of Inspected Fabric: Accurate measurement of the fabric length that has undergone inspection.
- Color Difference Display: Identification and display of color variations within the fabric.
- Auto-Generated Inspection Report: Automated creation of detailed reports summarizing the inspection results.
This real time data helps to make quick decision which is highly important.
- Data Analytics for Predictive Maintenance: In Quality 4.0, using data analytics is crucial. We collect a lot of data during fabric inspection. By using this data, we can create models for predictive maintenance. This helps us be proactive, reduce downtime, improve efficiency, and make sure our inspection equipment works at its best.
- Blockchain for Traceability: In fabric inspection, traceability is very important. Quality 4.0 uses blockchain technology to make an unchangeable record of every fabric’s journey during inspection. This makes the supply chain transparent. It helps quickly find where an issue came from and solve any quality problems.
- Collaborative Robotics (Cobots): In Quality 4.0, we include collaborative robots, also called cobots, in the fabric inspection process. These robots work with human operators. They handle repetitive and physically demanding tasks. This teamwork not only makes things more efficient but also reduces the chance of human mistakes.
- Cloud-Based Platforms: Quality 4.0 uses cloud-based platforms to securely store and analyze large amounts of data. This makes it easy for everyone involved to access inspection results and work together. Cloud-based solutions are scalable, flexible, and accessible, making it simple to make decisions based on data.
Advantages of Quality 4.0 in Fabric Inspection:
- Enhanced Accuracy: The application of AI and smart sensors in Quality 4.0 increases the accuracy of fabric inspection by reducing errors and enhancing the precision of fault detection.
- Effective Predictive Maintenance: Data analytics makes predictive maintenance possible, which lowers downtime and guarantees that inspection equipment operates at peak efficiency. This improves overall operational efficiency.
- Improved Traceability: Blockchain technology ensures transparent and traceable supply chains, making it easier to identify and address quality issues promptly.
- Data-Driven Decision-Making: Cloud-based platforms facilitate easy access to inspection data, empowering stakeholders to make informed, data-driven decisions for continuous improvement.
Challenges of Quality 4.0 in Fabric Inspection:
- Initial Investment: Implementing Quality 4.0 technologies requires a significant upfront investment in smart sensors, AI systems, and collaborative robotics. This might be a financial challenge for some businesses. It’s not advisable to install the system if a business deals with low-end garments and pays its employees less. This technology is more suitable for businesses dealing with high-end garments and paying their employees higher salaries. In such cases, the business is likely to achieve a quick return on investment (ROI).
- Skillset Requirements: The adoption of advanced technologies may demand a new skill set from the workforce, potentially leading to the need for additional training or hiring skilled personnel with high salaries.
- Cybersecurity Concerns: As fabric inspection processes become more digitized, there is an increased risk of cybersecurity threats. Ensuring robust cybersecurity measures is essential to safeguard sensitive inspection data.
- Integration Challenges: Integrating Quality 4.0 technologies into existing fabric inspection processes may pose challenges, and businesses must navigate potential disruptions during the implementation phase.
- High maintenance cost: Running the system effectively demands high maintenance charges for the machines and AI-based components, as it is entirely machine and AI-based.
Impact of Quality 4.0 in Bangladesh
Currently, we are at a stage where incorporating Quality 4.0 principles into fabric inspection can significantly improve our operations. But analyzing cost benefit complete adaptation of Quality 4.0 is challenging. But by partially digitizing our approach, we can transition from manual to real-time digital inspection reports, utilizing display boards for live recording and analysis. This not only aids in better decision-making but also streamlines supplier performance evaluations and record-keeping processes.
The adoption of these practices can lead to a notable reduction in manpower needed for data entry, thereby saving time in the analysis phase. While the initial investment in automated machines may seem high, it is crucial to recognize the long-term benefits. When compared to traditional processes, the cost-benefit analysis highlights the practicality and sustainability of this shift.
Conclusion
Considering the current challenges, such as rising daily expenses and workforce shortages, embracing Quality 4.0 in fabric inspection emerges as a strategic and sustainable solution. This transition ensures not only operational efficiency but also positions us for enduring benefits in the ever-evolving textile industry landscape.
In Bangladesh, the textile industry is facing problems with higher costs and demands from buyers for lower prices. To overcome these challenges and grow sustainably, it’s smart for the industry to adopt Quality 4.0 for long term benefit. This means combining new technologies with traditional methods to make better-quality garments. By doing this, Bangladesh can show that it’s forward-thinking and competitive on the world stage. To see fast returns on investment, it’s important to smoothly add Quality 4.0. This will pave the way for a better and more efficient future for the garment industry in Bangladesh.
- Written By–Mohaiminul Islam
- Quality Assurance Technologist at CSS-George at ASDA
- Ex-Student of Textile Engineering College, Chittagong
- You may love to read Fabric Inspection in 4 Point System
- Application of AI in Textile and Apparel Industry