GSD, general sewing data gives accurate data to set the standard minute value using the best method. It is a technique for methods analysis and the setting of time standards for the sewing industries. It can be used to evaluate operations within the textile industry in such environments as Cutting, Sewing, Examination, and Packing. General Sewing Data was devised by Methods Workshop Limited and is being continually developed by General Sewing Data Limited using an MTM database. Here we present General Sewing Data, GSD Concept, Codes, and GSD Sewing Formula.
It is a technique for methods analysis and the setting of time standards for needle trades work. It can be used to evaluate operations within the needle trades environment, such as cutting, sewing, pressing, examination, and packing. General Sewing Data recognizes commonly occurring motion sequences encountered in the needle trades environment and describes the motion utilizing codes, to each of which is associated with a definite time value.
General Sewing Data consists of 25 codes at the general level, which is supplemented by getting/Put Data and selected MTM codes to give complete coverage.The system has been structured to enable the GSD practitioner to produce a logical, accurate and consistent evaluation of method and time. The system must be applied correctly taking into consideration the applicable rules of GSD.
Contents-
- Introduction
- G.S.D handling codes
- General guidelines
- Sewing codes
- Distance codes
General Sewing Data-GSD
GSD was devised by Methods Workshop using an MTM database. It is a technique for methods analysis and the setting of time standards for the sewing industries. It can be used to evaluate operations within the textile industry in such environments as Cutting, Sewing, Examination, and Packing.
How does it work?
GSD recognizes commonly occurring motion sequences within the sewing industry and describes the motion utilizing unique codes that has a definite time value attached. There are 25 general codes, with additional Get and Put and selected MTM codes to give complete coverage.
How does it measure?
Each code has a time value attached expressed as TMU’s (Time Measurement Units). There are 2000 TMU’s in a Basic Minute. Additional allowances for rest, relaxation, fatigue and contingencies are applied to this to create Standard Minutes
GSD Concept
Operations within the sewing trade are generally broken down into 5 main categories:-
1) Get parts and match.
2) Pre-form and/or put part(s) to machine foot.
3) Sew parts together with various re-alignments or addition of parts between sewing bursts.
4) Trimming threads.
5) Putting parts aside.
Advantages of GSD
- Accurate
- Consistent
- Transferable between locations
- Easy to communicate
- Designed specifically for the sewing industry
- Method sensitive
- Predictive
- Eliminates “rating” element.
- Aids workplace layout design
GSD-Handling codes:-
The work performed by a sewing machinist can be broken down as follows:-
- Get part or parts and match
- Pre-form and/or put parts to machine foot
- Sew parts together align or add parts between bursts
- Trim threads
- Put parts aside
Handling codes:-The work performed by a sewing machinist can be broken down as follows:-
- • Get part or parts and match
- • Pre-form and/or put parts to mthe achine foot
- • Sew parts together, align or add parts between bursts
- • Trim threads
- • Put parts aside
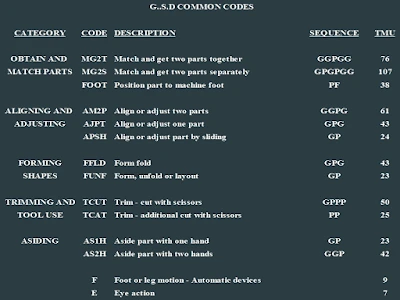
General guidelines: Always try to match the handling code to the get and put sequence being carried out. Gets – grasp and regrasp, and Puts – move pieces
1. Obtain and match parts
- Mg2s and mg2t are matched together at the machine bench and the code foot will still be required to present the pieces to the machine.
- Any other pre-forming of pieces can be inserted here using codes such as funf, ffld or apsh.
- Mape, mapi and map2 are for movements where pieces are matched together at needlepoint and do not usually need to be followed by the code foot.
2. Alignment or adjustment of parts
- Am2p is usually used for aligning at the end of seams.
- Ajpt is used to align along a seam, or for easy alignments funf (gp)
- Am2p and ajpt can also be used for aligning pieces before they are presented to machine foot.
- Apsh is used for movements around the needlepoint, for example, smoothing of panels. It is also used for pivoting work at the needle, and it must always be followed by the code f to lower the needle prior to continuing sewing.
- Am2p can also be used for button up.
GSD Sewing codes:-
Every code begins with “S” to indicate sewing. The code will then show the distance being sewn in centimeters. The next letter shows the degree of Guiding and Tensioning required:-
- N (Nil) – Straight burst on single ply
- L (Low) – Straight non-visible seam
- M (Medium) – Straight visible or curved non-visible seam
- H (High) – Curved visible/seam worked in confined space.
The last letter shows the stopping accuracy required:-
- A – Greater than 1cm (Along a seam)
- B – Within 1cm (Non-visible Backtack)
- C – Within 1/2cm (Visible Backtack or stop to pivot)
- Formation of shapes
- FFLD and FUNF are used generally to cover any number of similar movements.
- FFLD is used to form folds that require holding in position.
- FUNF is used for moving or folding parts that do not require regrasping afterwards.
- FCRS is used for smoothing actions where pressure is required.
- TCUT and TCAT are used for trimming threads, but can also be used for cutting fabric or poking out of collar points.
- AS1H and AS2H can also be used for bringing parts to the work area as well as asiding.
- MS1A is used for “sew to hold”, and MS1C for the formation of box tacks.
- GPCO and PPAL are used for pressing buttons such as use of Knuckle Backtack
- PPAL is used to push garment at foot to vacuum cutters/thread wipers and auto latchback. PPAL, TBLD, PPAL is used for manual latchback.
- MAP1 is mainly used to grasp and add one label to the machine foot.
- PPL1 or PPL2 are used for accurate positioning of parts to benchmarks, followed by E to check measurements.
- AS1H, APSH and FUNF have the same motion sequence of GET, PUT and similar TMU Values. Any of these three codes can be used as payment for moving or folding parts with one hand.
Therefore,- S11MA would indicate sewing an 11cm burst along a straight seam, with no specific stopping point. This type of code is usually used for Overlock Side seams.
Distance classified GSD codes:
Distance codes can be used to make GSD even more methods sensitive, particularly when engineering methods for workplace layout, or to analyse the benefits of mechanical improvements such as knuckle backtacks or new guides. Distances are grouped into classes as follows:-
Greater than | Movement distances in Centimetres Up – to and including | Code | Body Part moved |
0 cm | 5 cm | 5 | Finger |
5 cm | 15 cm | 15 | Hand / Wrist |
15 cm | 30 cm | 30 | Forearm |
30 cm | 45 cm | 45 | Arm extended / Shoulder |
45 cm | 80 | Upper Torso |
The code for distance can be added onto the standard GSD code, eg: MG2T45.
Workplace layout
Normal working area – finger, wrist and elbow movements.
Maximum working area – shoulder movements
The ideal layout should involve the operator not having to move further than the normal working area to complete her task.
The greater the distance, the greater the TMU Value:-AS2H5 = 31 TMU
AS2H45 = 45 TMU
AS2H80 = 52 TMU
Appendix of GSD codes, elements, and TMU values:
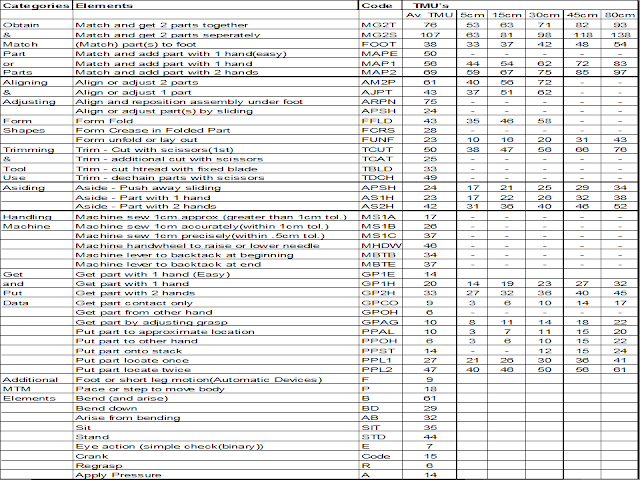
Conclusion:
Standard values set by GSD are accurate, the breakdown of elements is easily understood, and therefore consistency of values is achieved. Management/Supervisory staff can achieve an understanding of values within a short time of training.