Non-woven fabric manufacturing process in 3 Easy steps
Introduction
Whenever fabric manufacturing is concerned there are basically, three ways; weaving, knitting, and nonwoven process. Among those methods, the nonwoven is comparatively the latest and most high-tech process of fabric manufacturing. Nonwovens are defined as a web or sheet, of natural or man-made fibers or filaments, excluding paper, that are not being converted into yarns, and that are bonded to each other by many other several means. Here I present a details description Nonwoven Fabric Manufacturing Process.
Nonwoven fabrics are simply defined as web structures that are bonded together by entangling fibers either mechanically, thermally fusing the fibers, or by means of chemically bonding the fibers. When it comes to nonwoven fabrics it is not manufactured by weaving or knitting and do not require conversion of the fibers to yarn. Nonwoven fabrics are special kinds of engineered fabrics that are mostly single-use disposable or very durable fabric. They are used in numerous end applications of this kind of fabric such as baby diapers, adult incontinence products, wet wipes, surgical drapes, covers, etc. Let’s discuss on steps of the Nonwoven Fabric Manufacturing Process below.
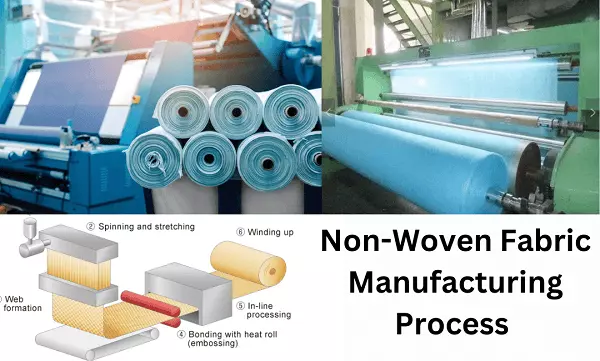
Steps of Non woven fabric manufacturing process
Nonwoven manufacturing is simply a continuous process in which web laying and web bonding are two major operations that are performed in two consecutive machines. So, the nonwoven fabric formation consists of three basic steps:
- Web Formation
- Web bonding
- Fabric finishing
1. Web formation
This step in nonwoven manufacturing is a crucial contributor of the end-use product performance. There are three common methods of web formation:
- A. Dry laid
- B. Wet laid
- C. Polymer laid
A. Dry Laid or Air Laid Nonwoven Process:
In this process, major staple fibers are used and involve three major steps. They are fiber preparation which is done by opening and mixing process, web formation conducted by carding or by air-lay processes and the last step is web stacking particularly done by parallel lay, cross-lay, and perpendicular-lay processes. Conventional staple fibers usually of the length of 12 to 100mm are used as raw material in the dry-laid process. Here, classical textile carding or air-laying machines are utilized to separate and orient the staple fiber mechanically for the creation of a fiber web.
B. Wet Laid Process
This manufacturing process of nonwoven fabric simply depends upon the paper-making process. The fibers can be dispersed in fluids, for that we can go for this process. Same as in the paper-making method, very short fibers dispersed in water are laid on a travel across perforated lattice. In wet-laid nonwoven manufacturing, to make the slurry the fibers are mixed properly with chemicals and then dissolved in water. Then, specific paper machines are used to remove the water off the fibers to create a uniform sheet of material like a web, which in the subsequent process is bonded and dried. Fibers with a length of less than 10 mm are preferable for the wet-laid nonwoven process and the resulting fabric has a weight varying from 10 to 540 g/m2. The wet-laid nonwoven process has advantages such as high productivity, great uniformity, and control of fiber orientation of properties, as compared to the air-laid process.
C. Polymer laid
Here, extrusions include spunbond (or spunlaid), melt-blown, and porous film systems. The fabrics that are manufactured by these systems are referred to individually as polymer-laid nonwovens. Extrusion-depended nonwovens are manufactured with machinery related to polymer extrusion, as used in the production of synthetic filaments. In a polymer-laid method, fiber formation, web formation, and web consolidation are carried out as an integrated operation. In the case of spunlaid fabrics, polymer granules are first melted and then the molten polymer is extruded through spinnerets. The continuous filaments that are formed are then cooled down and suspended onto a conveyor belt to form a uniform web. The filaments should be sufficiently warm enough so that the filaments can adhere to each other.
2. Web bonding
A. Needle punching
The process of bonding nonwoven web structures with the help of mechanically interlocking the fibers through the web is called needle punching. In this process, the barbed needles, mounted on a board, punch fibers into the web and then are taken out leaving fibers entangled. The arrangement of needles are such that they are spaced in a non-aligned arrangement to free the fiber as the needle board is withdrawn.
B. Stitch bonding
It is the process of combining the fiber webs with the help of knitting elements with or without yarn to interlock the fibers. There are numerous different varieties of yarns that can be used. Stitch-bonded fabrics are specifically used in home furnishings. Other applications include vacuum bags, geo-textiles, filtration, and interlinings. In many other uses stitch-bonded fabrics are taking the place of woven products because they are produced at a faster rate and, hence, the cost of manufacturing is considerably less.
C. Thermal bonding
In this process, heat is used to bond or stabilize a web structure that consists of a thermoplastic fiber. Here, all parts of the fibers behave as thermal binders, thus removing the application of latex or resin binders. This technique is majorly been used by the cover stock industry for baby diapers. For this technique, polypropylene has been the most preferable fiber with a low melting point of approximately 165C. Even it is soft to the touch. In this process, the fiber web is passed between heated calendar rollers, where actually the web is bonded. In most cases, the suitable and preferable bonding is by the use of embossed rolls which adds softness and flexibility to the fabric. With the help of smooth rolls, bonds the entire surface of the fabric which increases the strength, but reduces drape and softness.
D. Chemical bonding
This is the process of bonding a web by means of a chemical and is one of the most widely used methods of bonding. Here, simply the chemical binder is used on the web and is then cured. The most widely used binder is latex because it is inexpensive, easy to use, and very effective. Several other methods are also used to apply the binder including saturation bonding, spray bonding, print bonding, and foam bonding.
E. Hydro entanglement
In this process, fluid forces are used to lock the fibers together. This is done by fine water jets spread through the web, which is supported by the help of a conveyor belt. So, here the entanglement takes place when the water strikes the web and the fibers are deflected. The vigorous disturbance within the web causes the fibers to become entangled.
3. Fabric Finishing
As above it is mentioned that the manufacturing of nonwoven fabrics is carried out as either a continuous process, with the help of fiber or resin as the feed-in material and a roll of fabric as the result, or as a sequence of batch processes. Simultaneously, the fabric finishing process is carried out either in tandem with web formation itself and consolidation or offline as a separate operation. The common finishing process is slitting and winding for all nonwoven fabrics that are produced in roll form. For nonwoven fabrics, there are various finishing treatments given in order to enhance fabric performance of aesthetic properties. Performance properties basically include functional characteristics such as moisture content and transport, absorbency, repellency, flame retardancy, electric response, abrasion resistance, and friction behavior. Aesthetic properties deal with various characteristics such as appearance, surface texture, color, and odor. When it comes to nonwoven finishing processes it can be categorized as being chemical, mechanical, or thermal-mechanical.
A. Chemical Finishing
This includes the utilization of chemical agents such as coatings to fabric surfaces or the impregnation of fabrics with various kinds of chemical additives or fillers. In many cases, it is found that the chemical finishing is an extension of the binder application process. Generally, the coating process is performed to improve the properties of the nonwoven structure. When it comes to coating, it may be applied as a continuous covering or as a pattern. The coating material is frequently used as a solvent, aqueous solution, or molten polymer. When dealing with any nonwoven substrates, special care has to be taken because of the delicate nature of the structure itself or the arrangement of fibers on or near the fabric surface.
B. Mechanical and Thermal Finishing
The mechanical finishing process involves changing the texture of the fabric surfaces by physically re-structuring or shaping fibers on or near the fabric surface. There are various thermal finishing methods, such as calendaring, which enable structural changes to be permanently set into the fabric by the application of heat. To establish surface structures it may be done by embossing, compressive shrinkage (creping), and by creating loops or piles. Surface textures, varied from flat and smooth to raised and leveled, may be changed by calendaring, sueding, napping, polishing, brushing, and shearing. In general, it is found that the mechanical finishing processes operate relatively at speeds lower than web consolidation processes, and consequently are carried out offline or as separate batch processes.
Conclusion
It is the fact that woven Fabric, knitted, and tufted goods own the majority quantity of textile fabrics produced, while different fabric forming methods are available that do not require the preliminary making of yarn, or weaving or knitting steps. These products, which are known as nonwovens, are manufactured by the direct conversion of fiber to fabric. In today’s market, it is clearly found that nonwovens have a wide range of applications, which include home textiles, personal hygiene products, and technical textiles. Also, the special kinds of products that can be made by the nonwoven method, have a major advantage in that it requires relatively low cost of manufacture. Nonwoven fabrics may be manufactured by various techniques, but all generally include steps like web formation, bonding, and finishing steps. Currently, polyester is the leading fiber used in nonwovens. That’s all on the Nonwoven Fabric Manufacturing Process.
4. References
- 1. Nonwoven Manufacturing, Written by: New Cloth Market, https://www.technicaltextile.net/articles/nonwoven-manufacturing-7188
- 2. Types of non-woven fabric, manufacturing processes and applications, Md. Tanvir Hossain, August 23, 2020, https://www.textiletoday.com.bd/types-non-woven-fabrics-manufacturing-processes-applications
- 3. Paulapuro, Hannu (2000). “4”. Paper and Board grades. Papermaking Science and Technology. Vol. 18. Finland: Fapet Oy. Pp. 95–98. ISBN 952-5216-18-7.
- 4. “Process and apparatus for preparing a molded, textured, spunlaced, nonwoven web”, issued 2007-08-03
- 5. Nonwovens: Process, Structure, Properties and Applications by T. Karthik, R. Rathinamoorthy and C. Praba Karan
- 6. Nonwoven Fabric: Manufacturing and Applications by Rembrandt Elise
- You may love to read: 8 Key Applications of Nonwoven Fabric
- What is Bonded Fabric: Its Types, Application and Advantage
- An Overview of Disposable Surgical Gowns