Air Compressors in Textiles: Raised Performance, Reduced Costs
Introduction
The textile industry relies on effective production to meet rapidly changing market demands, and low pressure air compressors for textile industry play a vital role in powering equipment and machinery. Low-pressure compressors provide continuous power for textile production. They help producers meet growing demands by sustaining productivity. The article explains the role that air compressors play in textile production. It covers the types of compressors available and their efficiency and cost-reducing benefits. This guide shall assist a textile manufacturer in picking out an appropriate air compressor. Troubleshooting common problems can optimize production. In this article, we discuss details on Air Compressors in Textiles: Raised Performance, Reduced Costs.
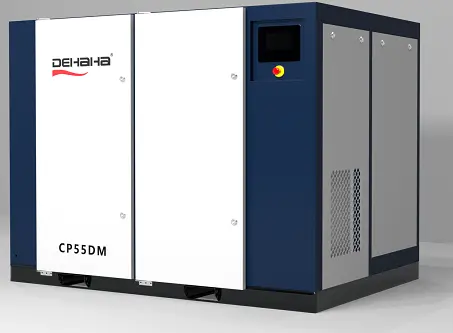
The Importance of Air Compressors in Textile Production
Air compressors are paramount in textile production. They are used to provide force for a host of operations and processes, some of which include:
The compressors help convert the raw fibres into yarn and spare fibres into threads.
Weaving:
Compressed air helps power looms and other weaving machines, allowing the threads to be woven into fabric.
Dyeing and Finishing:
Air compressors are power equipment used in dyeing, printing, and finishing textiles to ensure they look and feel great.
Material Handling:
Air compressors move fabrics and yarns around the factory and drive conveyor systems and material handling machinery.
To be more specific, air compressors are necessary for almost all of the processes required to manufacture textile products. They help move materials around the factory when producing yarn, fabric, and finished textiles.
Types of Air Compressors Used in the Textile Industry
Several kinds of air compressors exist in the textile industry for various purposes. Some are:
This operates at pressures of up to 100 psi, that is, pounds per square inch.
Used for light tasks like:
- Cleaning of fabrics
- Dusting of fabrics
Help keep fabrics and machines clean and dust-free.
Operate at pressures above 100 psi.
Used for heavy tasks like:
- Spinning raw fibres into yarn
- Weaving yarn into fabric
Provide more power for heavy applications.
Low-pressure compressors are used for light applications such as cleaning. The two-stage compressors, used for heavy applications, are used for spinning and weaving.
Advantages that come with using Air Compressors in Textile Manufacturing
Air compressors boost efficiency and save costs in textile manufacturing. They provide a consistent power source, reduce downtime, and enhance product quality.
More Efficiency:
- Air compressors provide a constant source of power
- Downtime reduced: Quantity of time when the machines are not working
- Increase productivity: The amount of work done in a given time
- Smoothly run factories to get more work done
Cost Savings:
- Air compressors use less energy than traditional power sources
- Reduce money spent on energy
- Save factories money on their energy bills
Enhanced Product Quality:
- Air compressors offer a constant source of power.
- Run products of consistent quality, the same every time.
- Help factories produce high-quality textiles.
Step-by-Step Guide on Choosing the Right Air Compressor
Step 1: Determine Your Air Needs
- Estimate your air flow and required pressure.
- Calculate the size of the factory and machinery therein.
Step 2: Choosing the Right Type of Compressor
- Low-pressure compressors for light applications such as cleaning.
- Two-cylinder models for heavy applications that involve spinning and weaving.
Step 3: Energy Efficiency
- Always go for compressors that consume less energy.
- The rating for energy efficiency should be high.
Step 4: Maintenance Costs
- See how much you will pay for maintenance for this compressor.
- See if spare parts can be found easily.
These steps will help you choose the air compressor for your textile production needs. When deciding, consider your needs, energy efficiency, and maintenance costs.
Getting the Most from Air Compressors in Textile Production
Follow best practices for maximum benefits. Ensure proper installation and maintenance.
Regular Maintenance:
- Inspect the air compressor regularly.
- Run Continuously.
- Avoid breakdowns.
Proper Sizing:
- Properly size your air compressor to meet your needs.
- Avoid under or over-powered compressors.
Energy Efficiency:
- Monitor how much energy you are using.
- Adjust the compressor settings to use less energy.
Common Problems and Troubleshooting Tips
Below are some common problems a textile manufacturer can encounter:
Air Leaks:
- Check for leakages in the system
- No energy was wasted after repairing the leakage
Compressor overheating:
- Ensure sound cooling systems are installed and
- Regular maintenance of compressors to replace worn-out parts
Conclusion
Air compressors increase productivity in textile production and simultaneously help reduce costs. Besides, they give an increased quality grade to the products, hence acting as essential equipment in industries. They make machines faster and more efficient, use less power, and decrease the amount of scrap material. The selection of a proper air compressor from a good screw compressor factory and adopting appropriate practices should be followed to enable optimum production and remain competitive in producing better textiles. Air compressors in the textile industry improve productivity and reduce the cost of production. They are essential to achieving success.