Alarm Tag/ Security Tag Attaching SOP in the Garments Industry
Alarm Tags also known as Security tags used in clothes. Alarm tags or security tags in clothing are anti-theft devices used by retail stores to prevent shoplifting. These tags are attached to garments and other merchandise, and they trigger alarms or damage the item if removed improperly. In this article, we discuss Alarm Tag/ Security Tag Attaching SOP in the Garments Industry.
To establish a standardized method for attaching alarm tags to garments, ensuring theft prevention and proper tagging procedures before shipping to retail outlets. This procedure applies to all personnel involved in the tagging process within the Finishing and Store Departments of the Garments Industry.
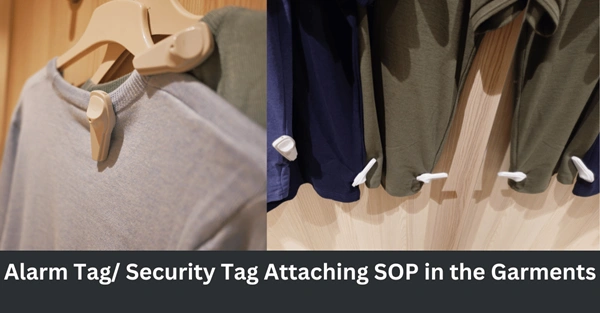
Alarm Tag/ Security Tag Attaching SOP in the Garments Industry
Responsibilities of Different levels:
- Quality Control Team: Ensure correct attachment of alarm tags.
- Supervisors: Oversee the tagging process and ensure compliance with the SOP.
- Line Operators: Execute the tagging process as per guidelines.
- Store Department: Manage the receipt, inspection, and delivery of alarm tags to the Finishing section.
Materials and Equipment
- Alarm tags
- Tagging guns
- Barbs
- Safety pins (if applicable)
- Work table
- Protective gloves
- Register book
- Lockable storage area for alarm tags
Working Procedure
Preparation
- Designated Room: A separate room will be designated for the alarm tag attaching process.
- Responsible Personnel: Only authorized personnel, whose pictures are posted in the room, are allowed to handle the alarm tagging process.
- Register Book Entry: All incoming alarm tags must be logged in the register book with details of the tags brought into the room.
5.2 Attaching the Alarm Tag - Select the Garment: Take one garment from the batch.
- Tagging Location: Identify the specified location for the alarm tag attachment.
- Tagging Gun Setup: Load the tagging gun with the correct size barb.
- Attach the Tag:
o Position the tag on the garment at the designated location.
o Insert the needle of the tagging gun through the garment fabric.
o Press the trigger to secure the barb, attaching the alarm tag firmly. - Verification: Ensure the tag is securely fastened and does not damage the garment.
5.3 Quality Check and Record-Keeping. - Visual Inspection: Inspect the attached tag for proper placement and security.
- Register Entry: Record the number of garments tagged in the register book, maintaining a tally of products tagged and balance quantities returned.
5.4 Handling Errors:
- Remove and reattach any incorrectly placed tags following the standard procedure.
5.5 Store Department Procedures
- Receiving Tags: Verify all received alarm tags as per the delivery note.
- Inspection:
o Check for any broken tags, ensure the color is correct, and perform a nickel test.
o If passed, store the tags in a secure, lockable area. - Delivery to Finishing: Provide tags to the Finishing section based on production needs and maintain a record of all deliveries.
- Safety Precautions
- Handle tagging guns carefully to avoid injury.
- Use gloves to protect your hands from repetitive strain.
- Ensure tags are attached safely to prevent hazards.
- Training
All personnel must undergo training on this SOP before participating in the alarm tagging process.
Alarm Tag/ Security Tag Attaching SOP in the Garments Industry