Cutting department
The cutting department is a major part of the garment manufacturing industry. This department, before bulk cutting, considers the following procedure: At first, they receive a Tag sample, and pattern and then receive fabric and relaxation. Also, they have received a marker from Product Development Center (PDC) department and pattern adjustment according to the marker and lay setting and fabric spreading on the table. After that, this marker spreads on the lay. Then machine cutting to the fabric. And then they are numbered and bundled for the cutting. So that the Sewing line matching to the two parts according to the pcs number and removes the fabric shade. Also, they are attaching the cut kit and trim cut to the bundle and storing the bundle in the cutting department. The flow chart of the cutting department is given here: Tag Sample & Pattern Sample → Fabric Receive → Fabric Relaxation → Size set marking → Pattern Adjustment → Marker preparation → Cut panel marking → Marker receiving → Lay setting and Fabric Receiving → Marker setting on lay → Fabric Cutting →Numbering & Bundling.
Fabric spreading: Fabric spreading is a process in the cutting department, done just before of cutting process as cutting is impossible with spreading. Fabric is to be separated according to dye lot before the spreading process, we need to know fabric quantity and height before the spreading process.
Recommended number of fabrics lay based on lay height in Cutting department
Fabric type | Lay Height | |
(Linen) | 200 Lay | 2½ ″ |
(T,C) | 300 Lay | 3″ |
(CVC) | 300 Lay | 2″ |
(Cotton Spandex) | 200 Lay | 2½ ″ |
(Stripe) | 200 Lay | 2½ ″ |
(Oxford solid) | 250 Lay | 3″ |
(Oxford stripe) | 250 Lay | 3″ |
(Twill cotton solid hard) | 180 Lay | 2½ ″ |
(Twill cotton solid soft) | 250 Lay | 2½ ″ |
(Corde) | 150 Lay | 2½ ″ |
(Denim Hard) | 150 Lay | 3″ |
(Denim Soft) | 150 Lay | 3″ |
(100% Cotton Check) | 200 Lay | 2½ ″ |
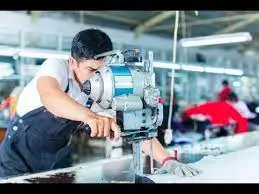
Cutting target calculations:
No. of Ply: 200 | Group manpower: 11 (Two Lay) | ||||||
Process Name | CT-1 | CT-2 | CT-3 | Avg. Cycle Time (min) | 20% allowance | Manpower | SAM |
Lay Setup time | 5.20 | 3.98 | 4.20 | 4.46 | 5.35 | 4 | 0.01 |
Laying time | 115.00 | 96.8 | 109.4 | 107.11 | 128.52 | 7 | 0.30 |
Marker time | 10.20 | 11.4 | 9.97 | 10.54 | 12.64 | 7 | 0.03 |
Cutting time | 36.56 | 40.6 | 39.98 | 39.06 | 46.87 | 4 | 0.06 |
Numbering time | 10.45 | 12.4 | 11.23 | 11.39 | 13.66 | 4 | 0.02 |
Bundle & unloading time | 12.73 | 11.45 | 14.63 | 12.94 | 15.52 | 4 | 0.02 |
Total SAM | 0.44 |
- Cutting Pcs Calculation per lay = Marker Pcs * Number of Ply
- = 15*200 =3000 Pcs
- Cutting Target = (Target efficiency*manpower*W.H*60)/SAM
= (0.8*11*10*60)/0.44
=12,055 Pcs
Cutting quality control
In the cutting section, the quality inspector first receives the cutting sample and design. Then they checked the marker, spreading length, cut panel measurement, and bundle numbering. If they are found not to be OK, then take corrective action. They also checked the embellishment and lot audit as per AQL. If pass the AQL, then cut pieces ready for the sewing line. A cutting quality flow chart is given here from the cutting department. The flow chart of cutting quality control: Receive cutting sample and design →Marker check →Spreading check→ Cut panel measurement (Top, middle and Bottom)→ Numbering and Bundling check→ Visual check of 100% cut panel.
In conclusion, we have to say cutting is an important department. So, quality and cutting accuracy are to be maintained in the cutting department.