Quality inspection
In any garment industry, different stages have different types of inspections for specific purposes for ensuring the best quality readymade garments. Every inspection point has a specific responsibility; this article is all about different types of quality control inspections in garments. Here we go; Different Types of Quality Control Inspection in the Garments Industry below.
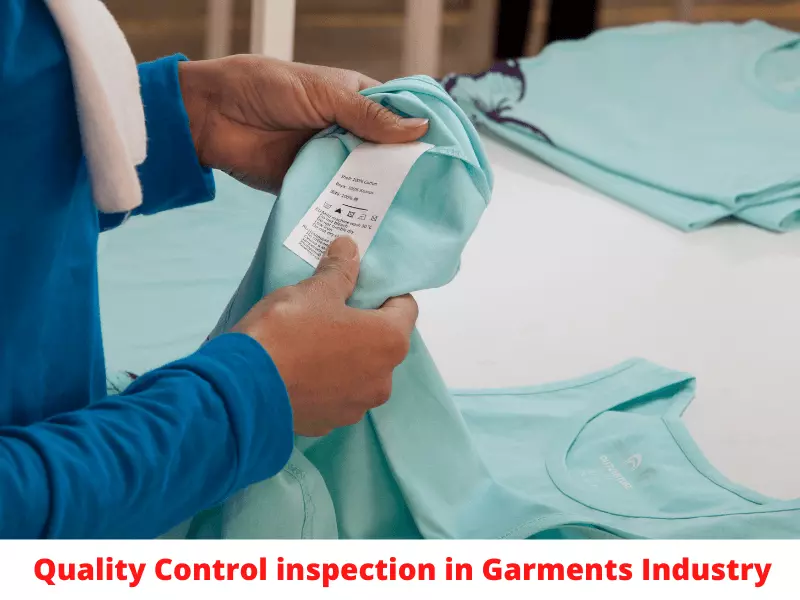
Types of Quality Control Inspection in the Garments Industry
Proto / other Sample inspection
At the development stage, the sample room QC supervisor shall analyze the construction of samples to ensure the sample-making method can proceed in our bulk production. The key intention is to avoid the rejection of all samples from buyers. So sample inspection is very important and prestigious to any garments manufacturer.
PP Samples inspection and P.P. Meeting
Before the PP meeting, the production sewing line shall copy the construction of samples from the buyer’s approval to ensure the sample-making method can proceed in bulk. The production department should then hold a meeting time to discuss all the order’s risks before starting the production. Every department including the sample room, cutting, sewing, finishing, QA, and PPC needs to attend. During the meeting, they will discuss the buyer’s comments, fabric & trims problem, sewing risks, workflow & delivery to ensure all requirements can meet our buyer’s requirements on time. In case of any difficulty/problem / high risk forecasted, an appointed representative will need to make some problem solving before starting production
Wash shade Blanket Inspection
Wash shade blanket(s) from all fabric rolls are needed especially for the denim fabric to ensure the washing effect can be achieved.
Shrinkage Test
Randomly select the fabric samples in each color lot per colorway to test the fabric shrinkage, then send the information to the pattern maker. According to the shrinkage report, the pattern maker will adjust the pattern to make a sample for the garment shrinkage test, then check the garment to finalize the adjustment
Fabric Inspection
Normally, if there has no special requirement, it will use the 4-point system to check at least 10% of the bulk fabric in each color and each lot respectively. The accepted total points per 100 square yards should be identified. A factory should use a 4 points system for applying to all fabrics, Inspection should have proceeded in face of the finished garment always and the acceptable maximum points per 100 square yards should be fixed as the standard guideline for acceptance reference. Besides the fabric defects, the inspector should also need to check for the bowing & skewing tolerance and color variance between each roll, and also check the same roll from end to end, side to side, and side to center color shade for comparison.
Trims and Accessories Material Inspection
When the material is received, check the construction, color, specification, quantities, etc., by the logistic department, QA will then check the quality of at least 10% of all material to ensure the quality.
Marker Inspection
Check the markers with consumption, panel placement, the total number of pieces, fabric layer height, arc & notches to ensure.
Cut Panel Inspection
100% panel check-in cutting department is necessary, sort out all the defective garments and panels with color shade before sending them to the sewing department. QA makes the random check afterward to ensure.
Inline Inspection
Roaming QC makes the inline inspection to each sewing operator, find out the defect immediately to chase the root cause to improve. In-process goods are 100% checked for the position of key parts to prevent no problem in the sewing process. The factory has a procedure to conduct 100% inspection for workmanship and visual defects at end of the line. Reports are maintained to review and issues are solved by the quality and production supervisor promptly. During the sewing line, a full measurement check for the completed merchandise in all sizes and colors with a report is necessary. Besides, 100% key part measurement with a record for the out tolerance data is also necessary for quality upgrades. A traffic light system is also a good example of inline inspection.
End Line Inspection
Production QC will make a 100% inspection with the measurement at the end of the sewing line to find out the defects at the earliest stage and inform the sewing line to improve immediately to prevent any continuous mistakes and any serious defects found at the final stage.
QA End Line Inspection
QA will make a random check at the end line stage to ensure the performance of production QC is functional. It can be called sewing end line inspection and ensuring the next stage gets a good product.
Presser Appearance Inspection
During the pressing stage, the presser has been required to make the observation and sort out the defective garment for repairing at the stage
Measurement Check/ Inspection
All products are to be measured after the pressing/ ironing process, so it is a 100% inspection process to ensure every garment meets customer measurement specifications.
Final Inspection in the Finishing Section
The garments finishing department has 100% final product workmanship inspection to ensure quality. All products go through 100% QC inspection for workmanship and measurement.
Sticker Inspection
Garments manufacturers perform an inspection just before folding to ensure hangtag, billboard, and UPC items are available and correct.
AQL Pre-final Inspection
Garments manufacturers perform pre-final & final inspections during the process. The pre-final inspection will make during the stage of just packing. Pre-final inspection is the preparation of the final inspection.
Final Inspection
It is the process of measuring, examining, testing, or otherwise comparing the unit of product with the requirement. The purpose of the final audit is to provide a quantitative level of quality for visual and functional appearance, measurement, and packing before the shipment. A final audit should take place whenever 100% of merchandise had been packed into the cartons with an accurate packing list.