Footwear Product and Component Safety Requirements
Footwear has a very high standard of safety in ALL categories. The responsibility of the Footwear factory is to ensure that the goods you supply are manufactured to our high standards of safety and quality. This section sets out specifically the requirements for products and components that are mandatory and those which are buyer/ customer Standards; in particular, the General Product Safety Regulations (2005), which state that it is the supplier’s and producer’s responsibility to sell safe products. This article is about the Footwear Product and Component Safety Requirements.
This refers to “products which under normal or reasonable conditions of use present no risk to the consumer, in particular children”. The following points cover the general quality assurance/safety requirements for all products, components, and trims. Any exceptions will be specified by the relevant technologist. If any trims are sourced from a non-approved source, then a written agreement /approval must be gained from the relevant Technical Manager of the customer and appropriate certification provided. Product and Component Safety Requirements in the Following:
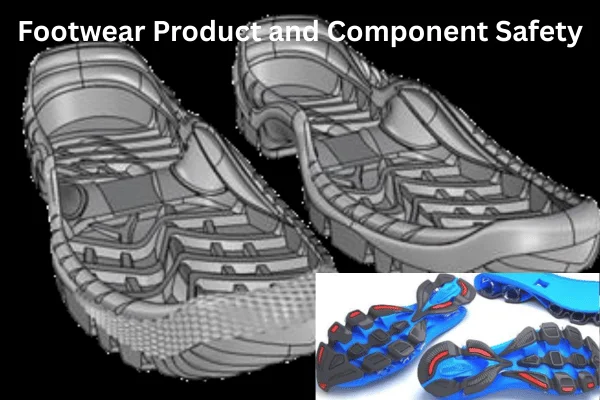
Footwear Product and Component Safety Requirements of all Parts
Soles– Footwear Product Safety Requirements
- A good lasting margin must be left & roughed sufficiently to ensure a good bond.
- Lasting margin should be prepped correctly before sole bonding for materials/style type
- Lasting margin should be minimum 13mm for adult footwear and minimum of 12mm for children’s footwear
- Ensure that regular, routine sole bond tests are carried out within each shift and every style change. These records must be made available on request if required
- For flat soles without lightener bars, avoid moulded “islands” as substitutes for bottom fillers. These tend to cause bridging in the bonding area resulting in sole bond failure
- Sole press dwell time must be a minimum of 10 seconds for cemented styles
- Carbon paper pressure tests should be carried out once every shift and changed with every style
- Sole bond test is not required if a side wall stitch has been added to the foxing edge. Full shoe flex test is still required (see Whole Shoe Flexing in Section 4.5 Uppers)
Lightener Bars
- The forepart bars should be positioned diagonally wherever possible to aid flexibility.
- All lightener bars should not infringe the lasting margin.
- Minimum width for bars in forepart is 3mm.
- Maximum spacing between bars is 15mm
Soling
- All soling materials must be tested for slip resistance
- All soles must have a slip resistance pattern embossed
- Where a heavy bottom pattern is a design feature, the minimum thickness above the cleats must be as follows:
- 3mm for solid PVC and TR (above 70 IRHD) & 4mm for expanded PVC and TR (below 70 IRHD)
Heels
Samples with wooden sample heels to be clearly labelled “Wooden Heel”
All high heels to be made from ABS high density plastic and attached with one of the following:
- Buttress nails
- Sonic staples
- Eclipse nails (only used in stacked leather heels)
- Screw fixing – can be used but only in conjunction with Buttress nails
Attachment Method–Footwear Product Safety Requirements
Nails
- The length of nails required depends on heel height, shape, and insole board thickness
- The length of the nail used for attachment must achieve at least 10mm penetration into the heel
- Buttress nails must be used for plastic heels
- Eclipse nails should be used for built heels (only used in stacked leather heels), but they must have a sharp point
- Buttress nails are suitable for heels made of compressed wood fibreboard 5/6 nails are preferred (with centre screw/nail)
- A centre screw or nail should only be used if the shank can be positioned correctly
- If a centre screw/nail used, this should be reinforced with additional grindery
- If the nail passes within 3mm of the shank recess in the seat board, insole reinforcement is advised, and this should preferably be a steel plate.
- Type, size, and pattern of grindery should be chosen to give the widest spacing over the heel seat, but never be closer than 5mm to the outside edges of the heel
- Depending on the heel shape, some grindery is inserted at an angle to reduce the risk of surface damage
- The foremost grindery should be 10mm or less behind the heel breast or effective heel breast
- On closed-back shoes, the rearmost grindery should be no more than 20mm from the rear edge of the insole
Staples
- If using ultrasonic staples, the largest staple is chosen such that the legs do not damage sides of heel
- The foremost point of attachment should be taken as the point where the centre line of front legs passes through the insole
Shanks
- Shanks to be made from hardened and tempered steel
- Shank width, thickness & performance is dependent on heel height
- Minimum width is 9.5mm for up to 75mm heel height. Use 13mm width for heels over 75mm high.
- The shank must be attached to the insole board by means of three eyelets, two in the forepart and one in the heel area
- Shanks must not exhibit “loose ends” which could work loose or penetrate the insole board
- All eyelets must penetrate the full thickness of the seat board. Shanks must not be taped or glued to the insole board
- Positioning of the shank from the heel should be as follows:
- Women’s – 12-20mm from rear edge of footwear
- Men’s – 25mm from behind the heel breast
- Front end of shank should be positioned relative to the breakpoint of the last:
- Less than 50mm heel height– 5mm behind breakpoint50-74mm heel height – level with breakpoint
- Above 75mm heel height – 5mm in front of breakpoint
Heel Types
• All heels 100mm high and over must be reinforced with a metal plate over the insole board (nail attachment method only).
Slender Heels
- Slender heels must be suitably reinforced with a metal pin (rod)
- The pin should extend as high as possible to maintain reinforcement throughout the stem
- The top of the stem should be surrounded by plastic
- A minimum of 3mm of seat thickness above the tension pin is required to prevent the pin from pushing through the heel seat when the top piece is inserted
- Where it is required the stem of the heel can be reinforced in either of the following ways: o A hardened, rolled, spring –steel tension pin moulded into the heel
- A hardened, steel rod integrated with the top piece, which is inserted into the heel after moulding
Low Stiletto’s
- For thicker heels below 50mm reinforcement may not be necessary
- Suppliers are to risk assess at product development stage
Cavity Heels
- For flat top pieces wall thickness must be no less than 3mm thick and wall thickness at the back edge of the heel wall should be at least 10mm to stop the top piece from falling into the cavity wall
- Seat thickness for heel attachment must be greater or equal to 10mm
- For autoloc top pieces plastic spigot should be non-circular to prevent turning in heel cavity
Built Heels
- Pins & staples to be driven from the top & bottom of the heel should be long enough to overlap by at least 2 heel lifts
- All pins should be within 8mm of finished heel
- Nails or tacks used to attach top piece should penetrate 8mm beyond the top piece
Insole Boards
Insole boards must not be attached to last with tacks or staples.
Insole Construction
- Insole board to be cut in correct direction
- Insole board design must be correct for product type
- Insole boards must be pre-mounded for styles as required, e.g. a heeled court or a structured ballerina
- For Ladies soft ballerinas, Active footwear and Sensitive Sole, a slotted insole board must be used
TOP PIECES
- Top pieces should carry a treaded pattern to prevent slip
- It is recommended for women’s shoes that Polyurethane top pieces are used
- Top pieces that are 10 to 25mm wide are generally Autoloc types or have moulded locating lugs (integral polyurethane spigots)
- Top pieces that are under 10mm wide must have a metal spigot
- Staples and pins used for attaching top pieces should penetrate at least 8mm into the heel (subject to heel height
Uppers
Vamps & Foreparts
- Panels within the shoes & pairs must be matched for shade & grain/nap
- Where checks or patterned upper/lining materials may cause miss-match between pairs, a level of tolerance must be agreed with the Commercial Team
- Leather to be cut in direction of least stretch – tight to toe
- No weakness in material where lasting pincers will grip
- Factory should code each panel for shade & appearance to prevent colour variation and panels to be paired up in production so lefts and rights match
- All vamp leather must be cut from prime areas of skin
- Flaws & defects are not acceptable
- Potential colour variation in leathers/materials must be highlighted to the Commercial and Technical team at development stages
- If variation in shade or grain/ finish is expected/ found in bulk, a colour card to display all variants within the batches must be submitted for approval
Facings
- Facings must be reinforced with a strong tape
- Blind eyelets must be used for the reverse of punched eyelet holes
- Facings must be secured with a small box stitch or stay stitch in the bottom corners
Gusset Elastic
- A double row of stitching should be used to attach the elastic to the upper material
- Where elastic is sewn into the upper there should be an underlay of 10mm
- For sewing the elastic into the upper the maximum stitch density should be 16 stitched per 25mm
- All gussets must be secured with lasting tape prior to lasting and the tape trimmed away after lasting
- Use round or narrow wedge point needles to ensure fibres are not damaged during stitching
Toe Posts
- Seams should be facing away from the foot for comfort – at the Tesco Technologists discretion
Moulded Toe Posts
- No sharp edges – all spew is to be trimmed away
- A washer may need to be applied to reinforce the toe post attachment
Jellies & Clogs
- No sharp edges – all spew is to be trimmed away
- Injected jellies and clogs can cause irritation, particularly to children if any sharp edges remain. Supplier must ensure the footwear is comfortable
Stitching & closing– Footwear Product Safety Requirements.
Sewing Threads
- Cotton thread must never be used
- No loose thread ends of un-cut floats longer than 5mm max
- Monofilament threads must not be used for seams or where there is a risk of direct contact with skin – unless approved by Tesco Technologist
- Thread ends to be trimmed not heat sealed
- Harsh or rough threads must not be used
- Chain stitch must not be used with heavy thread counts to reduce abrasion
- Standard bulk threads tend to fray and must be avoided. As an external decorative feature, double high twist thread products should be used instead
- Please use bonded nylon 6.6 or continuous filament polyester thread
- All sewing threads must be colourfast
- Top and bottom threads must be the same weight and type
- Care must be taken if pre wound spools are used that correct thread colours are selected
- Good colour match must be attained between thread and upper – unless a contrast effect is part of the design of the shoes
Needle Types & Stitch Densities
- For the preferred needle type, the needle size should be chosen to match the thread weight and appropriate for upper materials
Seams
- Seam allowances must be sufficient to produce a good level of seam strength
- Compliance required to EN71 Part 1
- Seams must withstand wear
- Seam allowance must be sufficient to reduce seam failure
- It may be necessary to increase some allowances to allow for materials prone to slippage, such as knitted materials
- All lockstitch seams must be correctly balanced and sufficiently tight to ensure the threads cross within the body of the material being sewn
- Lock stitch seams are suitable for all footwear upper seams, however all seam run ends must be back stitched by at least 4 stitches to prevent seams running back
Allowance for Lap Seams
- One component is laid over the other
- Normally the raw edge of the upper material is visible in the finished shoe
- Not always suitable for materials which fray
- Underlay of lap seams should be skived to avoid bulky seams
- One stitch row should pass through the full substance of both sections being joined
- A lockstitch is suitable for a lap seam.
Reinforcements– Footwear Product Safety Requirements
Topline Binding & Reinforcement Tapes
- Always use a top line tape with light or weak upper materials
- The widest possible tape to be used – minimum of 2.5mm
- Topline tape to be stitched along topline to ensure tape is fully effective
- Acute throat shapes, side seams, sharp corners or joins should be reinforced with a wide tape or stay material
- Stretchy and weak materials should be lined and reinforced as needed
Counter Stiffeners
- Strength/thickness of counter stiffener to be correct for product type e.g. ballerina requires a soft or no stiffener
- Where combined thermoplastic stiffener is used, it is essential to ensure good adhesion between the stiffener and the upper
- The lasting margin should be:
- 13mm for adult footwear
- 12mm for children’s footwear
Toe Puffs
- Toe-puffs should not profile through upper and must be edge skived as appropriate
- Woven type toe puffs should be cut on the bias
- When the upper is not lined, care should be taken to make sure that the back edge of the toe puff and upper are secure o For lined uppers – toe puff to be positioned 3mm from lasting margin edge (see diagram below)
- For unlined uppers – toe puff to be positioned 10mm from the lasting margin edge (see diagram below.
That’s all on the Footwear Product and Component Safety Requirements.
- You may love to read: Quality Control Workflow in the Footwear Industry
- Moisture Management Guideline for Apparel and Footwear Industry.
- Technical/ QMS/ Quality Audit Checklist of Footwear Industry.