The manufacturing process in the footwear industry requires raw materials for the production process. The material planning department in the Footwear Industry has to do so many things and coordinates with all the sections as required. This article presents details on the Operations of the Material Planning Department in the Footwear Industry.
At first material is received by the store team. For the purchase process, the article order is taken. Then, the product delivery date is known, raw material planning is conducted, and sourcing is done based on budget and availability. A supplier PI ( Proforma Invoice) is collected that contains price details and terms & conditions. Once management approves, the supplier is confirmed back with a PO number, which is registered into IFS and OMS by my MRP team.
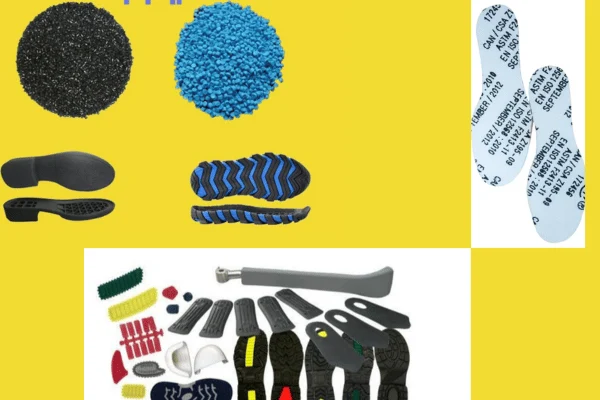
LC (Letter of Credit) is opened, and the commercialization team confirms the date of material arrival. Materials on arrival are checked by the store team and QC team, and on approval, the contents are unloaded. The materials are distributed to different warehouses based on their type and storage policy.
Production planning gives requisitions to the material store. The shop order is generated. DL sets a budget for each criterion of requisition. Packing instructions, Assortment section, and CD date are provided to the store team along with the color of material details. Every material is stored with a BIN card. A person from the store team will be in the production line for service-related changes and inventory updates from the floor to the warehouse storage system. Rest, step by step, Operations of the Material Planning Department in the Footwear Industry, in the following:
Operations Details of the Material Planning Department in the Footwear Industry:
A sequential step-by-step analysis of the operations of the Material Planning department is as follows:
- Customer order is received through MDL via OMS.
- A copy is stored in an Excel file, and a customer order is created in IFS by Design Lab (DL)
- Thus Shop order is created.
- DL produces a spec sheet from the customer MDL and then prepares a complete BOM (Bill of Materials) through routing and product structure (IFS).
- This BOM is connected to Shop Order, producing a complete SO with customer and size-specific materials.
- MRP team then collects the total material demand from IFS. On the other hand, the data pre-stored as an Excel file is updated by confirming/non-confirming the connecting SO. Thus, comparing IFS data, the not connected SO is separated, and demand for the main material is calculated by average consumption.
- Thus, material requirement planning is conducted manually by deducting the Order and Stock from the Total demand. Net Requirement = Total Demand – Stock – Order.
- After this, a purchase requisition is created in IFS.
- PR is released for 3 platforms. For International import, Pa O is requested via the ISC department, formerly known as the commercial department. For local sourcing, the PO is conveyed via the Accounts department. Lastly, the MRP team itself creates and sends a PO to AFLT.
- In return to this PO, import suppliers provide a PI (Proforma Invoice) and the MRP team initiates an LC (Letter of Credit) for the supplier, against which the supplier delivers the materials.
- Once, material arrives, the IQC team checks and validates. On their confirmation, the materials are stored in the bonded warehouses.
- In case quality issues are found, the MRP team takes action to address the issue with the supplier.
- You may love to read: Quality Control Workflow in the Footwear Industry
- Moisture Management Guideline for Apparel and Footwear Industry.
- Technical/ QMS/ Quality Audit Checklist of Footwear Industry.
- Footwear Product and Component Safety Requirements.