Quality Manager is to bring success to the company by ensuring that the products, performance, systems, and processes adhere to set standards and requirements. Having been a Quality Assurance Manager for many (could be 10+) years, a QA manager enhances his abilities in assessing requirements, investigating and setting up standards, performing actual systems testing, determining problems and needs, and resolving quality assurance issues of a manager’s special skills, One of my objectives is to further my expertise in the field of quality assurance, and I am confident I can do this best if I will be a part of a dynamic and competent environment. Know well about pattering / sewing and machine settings. Quality assurance manager to make assurance that all quality standards are followed on the production floor with the help of the quality team. This article is about the Job roles of Quality Managers in the Apparel Industry.
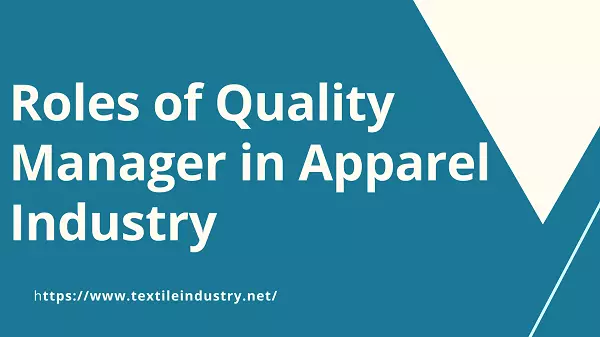
QA Manager Job Description in the Garments Industry
- Studying working sketch, specifications, and construction details of the garment to be made. Material selection and making the first pattern. Sewing the first sample garment or prototype – proto sample to see if a Design / Fit is successful; sending sample to the buyer. According to the buyer’s comments proceed with further production samples and maintain the T&A for sample approval for bulk.
- Interact QAs during all inspections Cross Checking & scheduling and reporting to the office head.
- Monitor quality parameters as requested by the client, Check fabric physical inspection to ensure the parameters Fab-Shades, Gsm, Shrinkage, Dyes defects, etc, Trims & Embellishment testing.
- Evaluating the Proto, Fit, and PP Sample and their manufacturing process, making sure it should be production friendly and making sure the sample follows the quality standard as per buyer requirements. Evaluating new clothing designs & Styling.
- Interacting with Designers team and CAD
- Production support, review, evaluation, and approval
- Producing specifications and production instructions
- Identifying suitable materials and accessories, Analyzing product returns and faults.
- Costing and budget management of the quality team.
- Ensure Technical specification Garment Construction
- General Quality Parameters in Sewing/Finishing/Cutting Garments. Manage Qa team & motivate, training to achieve results.
- Quality monitoring on machines as well as finishing the compliance audit.
- Coordination and push factories to get Fittings, Initials, Inline, and Midline & Final on time.
- Determining, negotiating, and agreeing on in-house quality procedures, standards, and specifications
- Assessing buyer requirements and ensuring that these are met online product
- Setting quality as client standards
- Specifying quality requirements of raw materials with suppliers
- Investigating and setting standards for quality improvement
- Ensuring that manufacturing processes meet standards.
- Working with coordinate production operating staff to establish procedures, standards, and systems
- Maintain technical / audit reports, weekly, and monthly reports submitted to management
- Determining training needs operators
- Encouraging change and improvement in performance and quality
- Directing objectives to maximize profitability
- Recording, analyzing, and distributing statistical information
- Supervising technical or laboratory staff.
- Interact with merchandise team needed approval and updates
- Ensure Technical specification Garment Construction
- General Quality Parameters in Sewing/Finishing/Cutting Garments
- Manage Qa team & motivate, training to achieve results.
- Evaluating the Proto, Fit, and PP Sample and their manufacturing process, making sure it should be production friendly and making sure the sample follows the quality standard as per buyer requirements.
- Quality monitoring on machines as well as finishing the compliance audit.
- Push and plan my team to get Fittings, Initials, Inline, and Midline & Final reports gets PASS one submission.
- Interact with merchandise team needed approval and updates
- Ensure Technical specification Garment Construction
- General Quality Parameters in Sewing/Finishing/Cutting Garments
- Manage Qa team & motivate, training to achieve results.
- Evaluating the Proto, Fit, and PP Sample and their manufacturing process, making sure it should be production friendly and making sure samples follow the quality standard as per buyer requirements.
- Quality monitoring on machines as well as finishing the compliance audit.
- Coordination and push factories to get Fittings, Initials, Inline, and Midline & Final on time.
- Ultimately, coordinating all quality issues are the main job Role of a Quality Manager in the Apparel Industry.
Finally, the job roles of a quality manager in the apparel industry are very critical and important. A garments factory depends on how it is quality assurance and control.
You May Love to read: Responsibilities of Quality Manager in the Garments Industry