Snap Button Safety is very important, so the attachment and the pinch setting have to be perfect to ensure product safety. The Snap button is a critical product safety issue. Below are the guidelines & Clarity for the root levels in the garments Industry for Snap Button Safety, Attachment, and Pinch Setting.
The Designer is responsible to consider the risk while designing the styling or generating the TP. The moment, the vendor gets the Tech pack to develop a pattern/sample /styling, must prepare to review the TP & initiates to do a risk analysis. This is a proactive attitude where Vendor can identify the error before it becomes a defect.
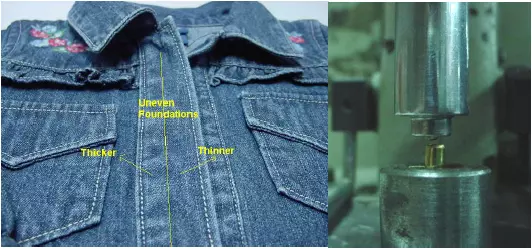
Risk Analysis
Risk Detail-we need to analyze the product in terms of risk . we need to update what are all the risk is there in the product & ensure to monitor those to avoid any risk to the customer. Purposes:
- To ensure the safety of the products
- To meet the expectations of our customers
- To protect the integrity of our brand
- Snap Button Positioning Foundation: Make sure that the foundation has 2 plies of fabric and 1 ply of interlining. This is the best-suggested foundation.
- Make sure that the snaps are not attached over two different foundation thicknesses.
- If an inter liner is not sewn in, the fabric can rip apart where the snap is attached which is causes the snap to come off.
- Make sure that there is no clearance between the fabric & Gripper
- Is the Gripper attached firmly? Check whether they will come off easily with a pull with the fingertips on the nails.
Supplier Selection and Technical Data Sheet
Snap button Quality most critical issue and it make always a big concern to the Client. We draw up a plan for the vendor & how can avoid the critical situation. Below are the 3 core initiatives:
Step 1: How to get the initial data sheet from the supplier:
Button booking stage, Vendor should send a garment or mock-up to the supplier with actual fabric and construction then the Supplier will examine the process and send the initial data sheet to the vendor.
Step 2: How to get the bulk datasheet:
During the bulk start, the vendor should inform the supplier to review the initial bulk attachment process
and set the machine set up. Finally, the supplier will review the bulk appearance and then provide the bulk data sheet. The supplier will train the machine operator, mechanics, and QAM, safety officer.
Step 3: How to confirm bulk production is safe:
At first, the vendor has to make sure the SNAP position placement foundation is even and the attachments process are same as the initial datasheet. The vendor must check all Snap one by one in front of Popper’s machine for button Quality and keep a record accordingly. The vendor will continue the process and they will check pull testing every two hours and keep the record for client review. For machine was set up in accordance with the pinch setting and it should be done every two hours using digital Vernier caliber.
Snap Button Pinch Setting
There is always a MINIMUM and MAXIMUM recommended thickness limit for every kind of fastener.
Basic Pinch: Determined by snap manufacturer based on the design of parts. This is what two components would measure when they come together without fabric between them.
+ Compressed Foundation Thickness: This is the minimum and maximum compressed fabric thickness where the snap will be located. These limits will vary according to the snap size and type.
= Setting Pinch: The total height of attached snap fasteners on fabric as measured on the specified location.
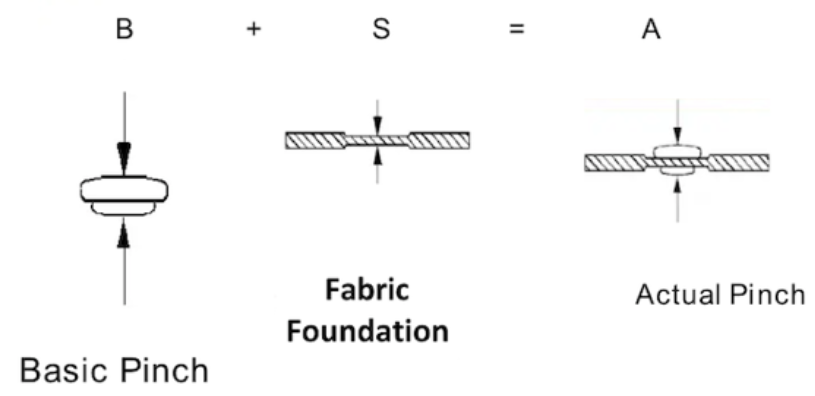
CFT + Basic Pinch = Setting Pinch | 15L Gripper, 0.011” + 0.085” = 0.096”, (Tolerance +/- 0.003”)