Different Types of Waste in The Spinning Mill Production Process
Spinning waste includes all items that people no longer have any use for, which they either intend to get rid of or have already discarded. Different types of wastes are generated in different processes of spinning. The spinning waste’s name and percentage are given below. Spinning waste In practice we can define wastage as, Input – Output = Wastage. That means whatever we cannot use, we have to throw away. In this article, we discuss Different Types of Wastage in The Spinning Mill Production Process.
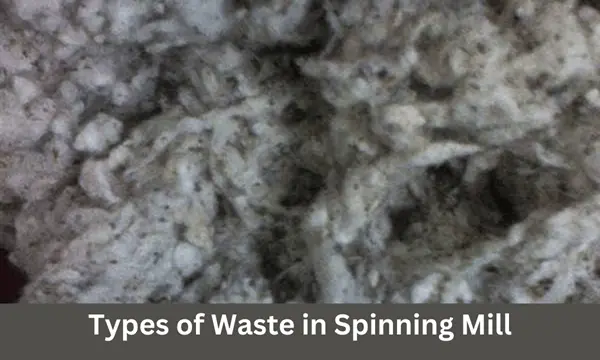
Different wastes are generated in different production processes of spinning. The wastes are distinct of two types: (a) The Process wastes taken out in the blow room, cards, and combers which accounts for nearly 80% of the total waste losses in cotton spinning and 50% in man-made and blends spinning. The process waste is decided by arriving at the optimum levels required to achieve the desired yarn quality.
(b) The product wastes which are incurred at each stage of processing, the control over product wastes has to be exercised through effective floor supervision. A list of waste and percentages in different production processes of spinning is given below:
Name of Spinning Wastes with Percentages:
Several types of waste are found during the processing of row cotton in spinning mills 12-13% wastage is produced for the card process and 25-30% wastage is produced for the combed process. The names of different waste are given below,
- Blow Room (4-5%): Droppin-1, Droppin-2, Fine dust
- Carding (5-6%): Flat strip, Licker-in, Vacuum waste.
- Drawing (0.5%): Filter Waste, Sliver waste, Sweeping dust
- Lap Former (0.5%): Sliver waste, Lap waste
- Comber (10-20%): Lap, Sweep, Noil
- Simplex (0.5%): Sliver, Roving, Apron Clearer waste, Sweep waste
- Ring Frame (3%): Roving, wooden roller clearer, Bonda, Soft waste, Pneumafil, Sweeping.
- Winding (0.5%): Hard Waste, Sweeping, Invisible waste
- Rotor Spinning: Pneuma dust, Hard waste, Sliver waste, Soft waste
Wastage Reduction Procedure/ Factors for Wastage Reductions:
- Right and Quality Raw materials selection
- Spindle speed
- Setting(Rollers, R/T, Traveller cleaner etc)
- Twist of yarn
- Machinery condition
- RH% and Temperature
- Proper material handling
- Adequate supervision
- You may love to read: Waste Disposal Policy in the Garments Industry